Densurf DA 4010 Make an Effective Difference at Dispersions
Black is not actually a color. Black is only a state of colorlessness caused by the lack of light rays reflected from a given surface. So how do you obtain black color? In nature, black color can be obtained from nuts, chestnuts, and roots of certain oak trees. Artificially, pigments like iron oxide or carbon black are also sources of black color.
Nowadays, the most common pigment used to achieve black color is carbon black. Carbon black is preferred not only because of its capacity to achieve black color but also carbon black’s ability to absorb sunlight, resist UV rays, and resist heat.
Some industries carbon black is commonly used are rubber, paints and coatings, ink, leather, plastic, and textile. Carbon black production depends on decomposing (pyrolithic) hydrocarbons or herbal oils with heat.
Depending on the manufacturing process, carbon black’s properties such as color tone, particle size, surface area, and pH can be adjusted.
[caption id="attachment_142785" align="aligncenter" width="229"]
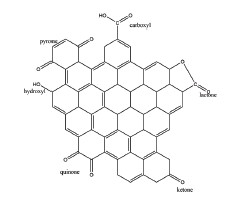
Figure 1. Chemical structure of carbon black[/caption]
Carbon black pigment’s chemical structure is given at Figure 1. Carbon black’s structure contains ketone, hydroxy, quinone, lactone, pyrone, and carboxylic acid functional groups.
Carbon black has a hydrophobic surface. Both the small particle sized (generally 20-30
nm) carbon black pigments and the interaction between carbon black’s functional groups cause flocculation in liquid systems.
Separating clumped carbon black particles in liquid system and creating a new intersection
between pigments and liquid is called dispersion. Dispersion process is an important step in paints and coatings industry.
Mainly polymeric dispersion agents are used to disperse carbon black in liquid systems. Pigment dispersion is achieved through the steric hindrances and electrostatic forces present in the dispersion agent’s composition.
Densurf DA 4010, is a polymeric dispersion agent. While Densurf DA 4010 polymer’s anchor group envelops the pigment particle, it causes steric hindrance with its tail group. Therefore, Densurf DA 4010 blocks the increase in viscosity of the system while maintaining stability in the system.
Figure 2 schematically illlustrates the dispersion of carbon black with Densurf DA 4010.
Whilst polymeric dispersion agent’s tail length interrupts the interaction between carbon black pigments, it is also important to consider to interactions between polymeric dispersion agents.
Polymer’s tail length should be optimized to hinder pigment-pigment interaction while
preventing polymers to interact with themselves. Interactions of dispersion polymers when the chain length is increased is demonstrated in Figure 3. Carbon black is used in universal resin systems for both organic and inorganic pigments.
While synthesizing Densurf DA 4010, 6 Sigma methodology was utilized to optimize acid / amine ratio, anchor groups design, and length of tail group.
[caption id="attachment_142787" align="alignleft" width="263"]
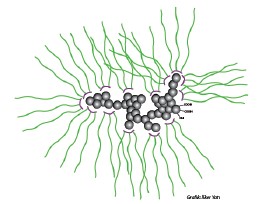
Figure 3. The effect of the length of polymer’s tail group to the dispersion[/caption]
[caption id="attachment_142786" align="alignright" width="300"]
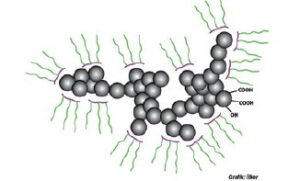
Densurf DA 4010 and carbon black dispersion[/caption]
In dispersion processes, using the right amount of dispersion agent is just as important as choosing the right dispersion agent. When a dispersion agent is used excessively, anchor groups interaction with each other prevents the system to remain stable, causing
flocculation and precipitation.
When used very little, anchor groups do not wrap up the pigment enough, causing the same problems.
When dispersion agent amount is determined, % s.o.p (solid on pigment) ratio
can be utilized. This ratio shows variety for every different pigment. While significantly smaller ratios are utilized in inorganic pigments, organic and carbon black pigments benefit
from higher s.o.p. ratio.
[caption id="attachment_142788" align="aligncenter" width="320"]
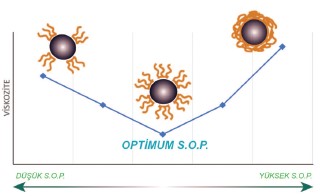
Dispersion agents optimum amounts
effect on systems viscosity[/caption]
Roughly, optimum dispersion agent amount can be estimated by dividing the pigment’s surface area by 5. Dispersion agent’s optimum amount’s effect on system’s viscosity is shown at Figure 4. For carbon black, % s.o.p ratio varies between %30-100 depending on the paint formulation and surface area of the pigment.
% s.o.p= (dispersion agent’s solid content / pigment amount) *100
Ratio study should be conducted at mill-base to discover optimum s.o.p ratio. Solvent-based paint formulation is given at Table 1 for Densurf DA 4010.
[caption id="attachment_142789" align="aligncenter" width="772"]
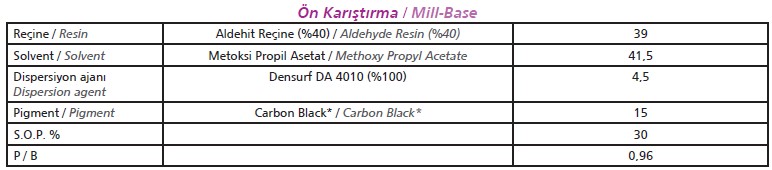
Table 1. Solvent-based paint formulation for Densurf DA 4010[/caption]
[caption id="attachment_142790" align="aligncenter" width="784"]

*Particle Size: 25 nm, surface area:110 m2 / g, pH:4[/caption]
Samples prepared according to the formulation given at Table 1 was tested for fineness of grind, viscosity, rub-out test, and shine. All samples were kept at 50ºC for 2 weeks before testing for their viscosity again. No viscosity increase has been observed. After 4 weeks, all the tests were repeated and all the results came out parallel with each other.
Viscosity measurements are given at Figure 5. Gloss and DOI (Distinctness of Image) measurements are given at Figure 6. and rub-out test results are given at Figure 7.
[caption id="attachment_142792" align="aligncenter" width="374"]
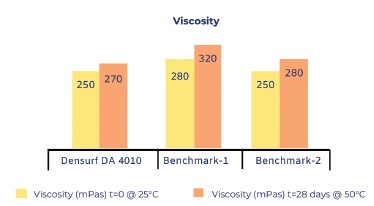
Figure 5. Viscosity measurements[/caption]
[caption id="attachment_142793" align="aligncenter" width="300"]
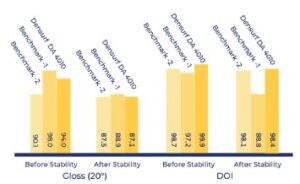
Figure 6. Gloss and DOI (Distinctness of Image)
measurements[/caption]
[caption id="attachment_142794" align="aligncenter" width="736"]
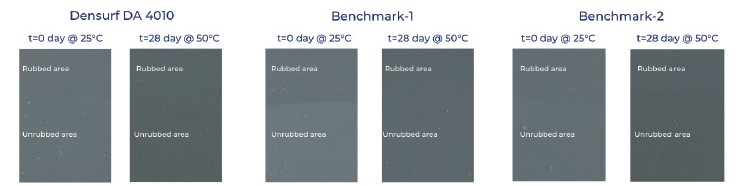
Figure 7. Rub-out test results[/caption]
References:
https://www.anatoliakimya.net/Tr/temel-kimyasallar/karbon-siyahi-4567.aspx
https://densurf.com/media/rhkdarck/leaflet-da-4010.pdf
https://www.orioncarbons.com/en/oec_3065_r7_carbon_black_pigments_tech_data_v2_5_10_19.pdf
https://en.wikipedia.org/wiki/Carbon_black
Aylin Aydemir Hüseyin Eren
R&D Specialist
Denge Kimya
Senior Application Specialist
Densurf
Hüseyin Eren
R&D Specialist
Denge Kimya