Line Type Automatic Filter Unit
Our company finished the prototype studies of self cleaning line type automatic filter units, now our close customers started to try it on their facilities to end product. Below we presented our new filter unit details.
About The Line Type Automatic Filter Unit: What Is?
It is a liquid filter developed for filtering the solid particles in the liquid and obtaining the product in the desired micron range, so that the liquid products or semifinished products produced in industrial facilities can pass the quality control criteria before they are filled
into the storage tanks and/or packages.
This filter; It is connected to the pipeline where the liquid is transported, the liquid product enters the filter and comes out after being filtered, there is no need for an intermediate waiting tank before or after the filter.
Its dimensions are optimized so it occupies minimum space inside the facility.
The filter element inside the filter body can filter a minimum of 25 microns.
The most important feature is; The filter has a selfcleaning feature. In this way, the continuous filter element (cartridge, filter cloth, etc.) does not have to be changed. In this way, a great advantage is obtained in terms of operating costs due to consumable savings,
and there is no loss of production time in the enterprise since there is no filter element replacement operation.
Usage:
It is effectively used in all enterprises that produce liquid products and semi-finished products, as well as in all enterprises that use liquid semi-finished products in their production and want to filter them before adding them to the process. It can be easily used in all sectors where liquid products need to be filtered, especially paint, resin, textile chemicals, food products, chemical products. Production capacity may vary depending on
the maximum allowed particle size and product viscosity in the product after the filter.
Working Principle of System:
Figure 1 shows the front view of the line type automatic filter. If we want to define the filter sections in general terms;
• Liquid product to be filtered from the upper left; enters the filter system,
• The liquid passing through the automatically controlled ball valve at the top right enters the filter body,
• With this automatically controlled valve placed before the filter, the liquid flow from the main line is cut off during maintenance and cleaning.
• Inside the filter body, there is a filter element made of stainless steel in the form of an open top and bottom cylinder.
[caption id="attachment_136939" align="aligncenter" width="533"]
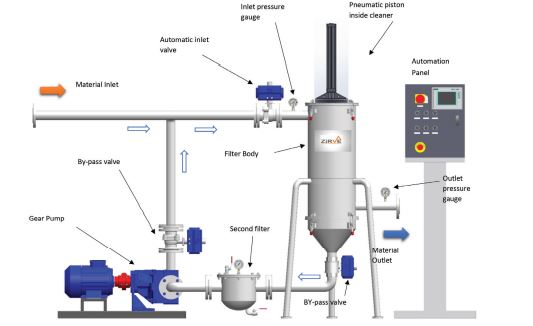
Figure 1: Line Type Automatic Filter General View.[/caption]
• The liquid to be filtered is filtered by passing through micropores from the inner surface of the filter element to the outer surface.
• The filtered liquid comes out from the right side of the body and continues the process.
• Particles that cannot pass through the filter begin to accumulate on the inner surface of the filter.
• Thanks to the pressure gauges at the inlet and outlet of the filter body, the pressure difference is measured in the filter, when it exceeds the set value, the pneumatic piston on the filter body is activated, the cleaning disc, which will scrape the inner surface of the filter element, moves up and down, and thus the particles accumulated on the inner surface of the filter are scraped off the filter. body accumulates in the lower cone. Depending
on the pollution rate of the product to be filtered, the accumulated particles are automatically transferred to the by-pass line by opening the valve under the cone momentarily after a certain period of time. The products that pass through the coarse
filter in the by-pass line are pressed to the product inlet line by passing through the gear pump to be pumped back to the product inlet line. The purpose of the by-pass system is to transfer the products that escaped unfiltered during discharge back to the filter inlet.
• The coarse particles come to the fixed coarse filter along the line extending to the right from the bottom of the filter, and some of the coarse particles are retained there,
• The coarse particles accumulating in the static coarse filter should be cleaned manually at regular intervals.
• The automatic filter cleaning operation we are trying to describe takes place in a very short period of time. Even at this time, the filter system continues its normal product filtration.
• After the automatic cleaning process, the valve under the filter closes, the gear pump stops and the filter system continues its normal operation.
• Self-cleaning of the filter takes place thanks to pressure sensors, automatically controlled valves and PLC controlled automation system in which all these electronic devices are controlled.
Technical Details of Unit:
• All metal parts in the system, especially the surfaces that come into contact with the liquid product, will be determined according to the chemical properties of the liquid to be filtered and the hygiene conditions of the facility.
• The metal parts in contact with the product will be produced from AISI304 material.
• Pipe connections are generally flanged type.
• Automatically controlled ball valves are a part of the automatic control system, and are also installed in the system to facilitate the dismantling of equipment, especially during maintenance and cleaning.
• Pressure sensing sensors measure the pressure at the inlet and outlet and send data to the automation system to calculate the pressure difference. At the same time, pressures at different points of the system can be observed with the analog pressure gauges installed in the system.
• The filter element is mounted inside the filter body in a completely leak-proof manner with the help of gaskets on the lower and upper flanges. The filter element inside the filter body is specially designed and manufactured entirely from stainless steel pyramidal wires.
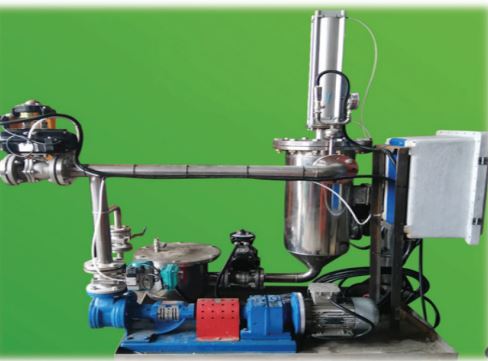
[caption id="attachment_136945" align="aligncenter" width="201"]
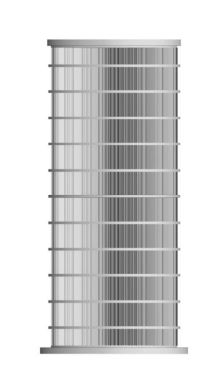
Figure 3: General View of
Stainless Steel Filter Element[/caption]
[caption id="attachment_136946" align="aligncenter" width="425"]
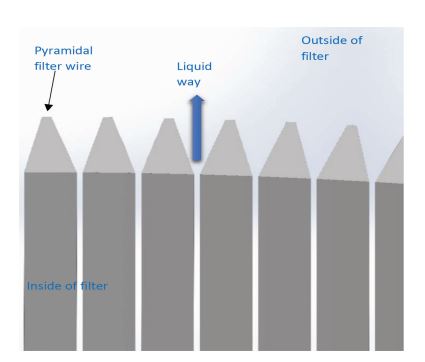
Figure 4: Detail View of Stainless Steel Filter Element[/caption]
• Thanks to the pyramid-section steel wires, an effective filtration is ensured, the particles passing through the filter slots can be easily removed from the system without being jammed again, so the problem of filter clogging is not experienced in this filter system.
• Solid particles that cannot pass through the filter element slots begin to accumulate on the inner surface of the filter, the difference between the pressures detected by the digital pressure sensors at the filter inlet and outlet is continuously calculated by the automation system and as soon as the limit value passes; PLC system; starts the automatic self cleaning procedure.
• With the start of the automatic filter cleaning procedure, the automatically controlled discharge valve under the filter opens at the same time, the filter scraper mechanism starts to rotate and discharges the accumulated particles under the filter, simultaneously the gear pump operates and the liquid passing through the coarse filter is pushed back to the main filter inlet line.
• The automatic filter cleaning procedure is a very short operation. During filter cleaning, the filtering process continues the same, only some unfiltered liquid with coarse particles also escapes into the discharge system, this escaping liquid is returned to the system and filtered.
• Inside the static (coarse) filter, there is also a filter with larger pores than the main filter. There is no automatic cleaning system in the static filter, so the particles kept here must be cleaned manually at regular intervals.
• The gear pump placed after the static filter further increases the pressure of the liquid at pressure equal to the system pressure in the discharge line, allowing the liquid to be injected easily into the ‘T’ connection in the main line.
• Values such as system operating pressure, inlet and outlet pressure difference limit value, filtration flow rate, operating temperature of the system, product viscosity, average particle size of the filtered product vary according to each business and each product.
• Our Inline automatic filter system provides filtration up to a minimum particle size of 25 microns.
• This filter can be used in liquid lines operating with a maximum pressure of 16 bar.
• This filter system is designed to be resistant to filtering liquid products at a maximum temperature of 200
0C.
Advantages; According to Classical Filter Process
• While it is necessary to change cloth filters or cartridge filters frequently in classical systems, the filter element can be used for many years in this system. In this way, both consumables are saved and there is no interruption and time loss in production as there is no time to change the filter element. More production is made compared to classical systems.
• In this system, since the filter is constantly cleaning itself, the same quality product is always obtained.
• Since the filter does not have a clogging problem, the process pumps that pressurize the main line are not forced, thus saving energy.
• Especially the surfaces of the filter that come into contact with the liquid can be easily disassembled and reassembled in a short time after maintenance and cleaning.
Yiğit Dölen
General Manager
Zirve Proses
.