The combination of synthetic resin binders and fillers (aggregates) of the kind familiarly used with cement yields a building material of mortarlike consistency which, after curing, has properties unattainable by conventional materials.
The outstanding characteristics of this mortar, which is also called synthetic resin concrete, are its extremely high mechanical strength,
chemical resistance, short curing time and excellent adhesion to traditional building materials.
The binder to sand ratio and the workability are important for the properties and economy of synthetic resin concrete. The lower workability limit is given by a resin content of 2%, but such a material will probably be of no more than limited interest because it is not very strong but permeable to air and liquid.
The strength rises as the proportion of resin increases. The maximum is reached at 15% binder; no more is therefore necessary because more resin reduces the strength. Still, a synthetic resin concrete with 20% binder has a compressive strength of about 75.0 N/cm
2 and a transverse strength of about 25.0 N/cm
2 while normal concrete has a compressive strength of 25.0 N/cm
2 and a transverse strength of 7. 0 N/cm
2.
Synthetic resin mortars with a higher resin content may well have a specific practical interest because they have greater flowability and are self-levelling.
This gives good workability which makes high laying rates possible. The most usual synthetic resin mortar consists of 10 - 15% by weight resin and 85 - 90% sand.
When articles and structures to be coated are continuously exposed to severe conditions, paints and varnishes are insufficient for permanent protection. Here synthetic resin mortars can be recommended because, given suitable resins, they combine very good mechanical strength with good chemical resistance.
There are two principal groups of synthetic resin mortars:
1. Trowelling mortars,
2. Self-levelling mortars,
The two groups are characterised by the difference in the binder content and the particle size composition of the fillers.
Trowelling mortars (high filler content 85% or more) are normally used at thicknesses of 5 - 10 mm. Cured synthetic resin mortars produced to these formulations have the following properties:
• High mechanical strength like compressive,
• Transverse and impact strength.
The low coefficient of thermal expansion means that the mortar can still be laid at low temperatures. It can only be applied with a suitable tool like a trowel; some formulations must be compacted after the application. Specially modified formulations enable synthetic resin mortars to be applied to vertical surfaces.
Self-Levelling mortars (85% filler or less) are normally used at thicknesses of 3 - 6 mm. Synthetic resin mortars produced to these formulations can be laid at a fast rate; only rough levelling is necessary on horizontal surfaces; these mortars resist impacts less well than trowelled mortars. in contrast to low-binder mortars their surface is smooth, glossy and impermeable to liquids. If there is any surface tack after the cure, it can be removed with water.
For a non-slip surface, the coating must be sprinkled with sand before the cure. If the self-levelling mortar contains a high proportion of resin, it has, after the cure, a larger coefficient of thermal expansion which may be three to five times as large as that of concrete or iron.
It means that this mortar cannot be used on surfaces exposed to low temperatures (0⁰C or lower). When the coating is more than 2 mm thick, stress conditions occur which may cause the coating to crack off.
These stresses have not been observed with coatings less than 2 mm thick. Producing a synthetic resin mortar is as simple as can be. If the mixing ratios of the resin components have been satisfied and the mortar has been properly mixed in the absence of water, it will give satisfactory results.
Standard values for application rates are given below; they may vary a little, depending on the surface condition.
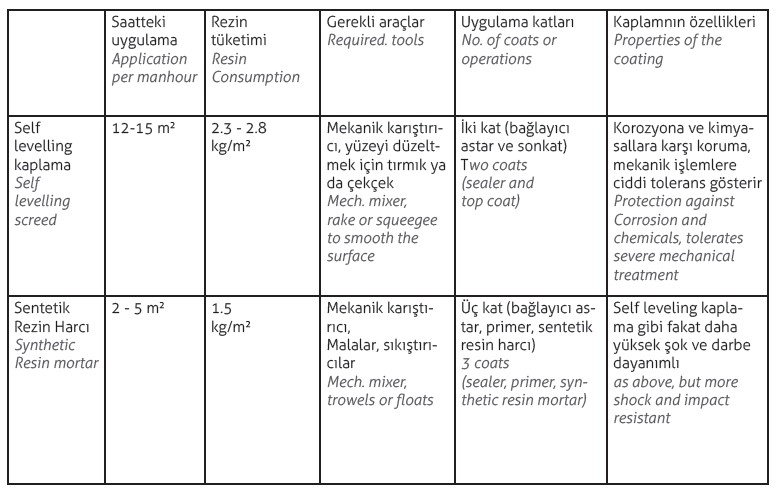
It is important for the quality of the coating to stick to the right working conditions. The resin systems attain optimum characteristics at the mixing ratios given in the formulations.
Only truly uniform mixtures of the two components react satisfactorily throughout the mortar.You should therefore be reminded of the need for thorough and adequate mixing.
Mechanical mixers with edge scrapers and preferably of 50 - 80 litres capacity are required to make a good synthetic resin mortar. The mixing effect of gravity mixers is not adequate. First the appropriate amounts of epoxy resin and hardener are uniformly mixed in a mechanical mixer.
Then the filler is stirred in and kneaded until it is evenly wetted. Mixing takes about five minutes. In order to avoid excessive air entrainment while the mortar is mixed, 0.5 % silicone oil on the binder may be added. Some of the most suitable silicone oils are silicone oils from companies such as Wacker, Bayer or Byk.
The addition of silicone oils is particularly recommended for self-levelling synthetic resin mortars because entrained air migrates to the surface where it forms blisters after the coating compound has been laid.
As a cold setting system the binder has only a limited pot life, varying between 20 minutes and six hours, depending on the type of hardener. The pot life is also significantly affected by the size of the mix and the ambient temperature.
Fairly large batches are best split up into smaller lots after mixing in order to avoid local overheating which would accelerate the reaction. The good adhesion of the binder may become a disadvantage during the laying of the synthetic resin mortar, depending on the formulation.
After a while the mortar sticks to the trowel which makes clean smoothing difficult. Brushing the trowel with a solvent provides a cure - 2-ethoxyethanol has proved effective. This difficulty does not arise when the formulation contains paraffin oil. De-aerating the mortar with silicone oil also reduces clinging to the trowel.
When mortars with a low resin content (10%) are laid, a primer or bonding agent is recommended. The resin/ hardener mix used in the mortar, but without the fillers, can be used as a bonding agent which is thinly applied to the surface before laying the mortar.
In practice it serves as an adhesive between the background and the low-binder mortar. A filled bonding agent has application advantages.
Quartz powder and Aerosil make suitable fillers which prevent the bonding agent from striking through to the surface of the coat to give it a mottled, greasy appearance.
The bonding agent can be coated with synthetic resin mortar as soon as it has been applied. However, when the mortar contains about 15% binder there is no need for a bonding agent.
The most careful attention must be paid to the preparation of the surface before even the synthetic resin mortar or bonding aid is applied.
Only a perfect surface guarantees perfect adhesion of the coating. If a poor concrete floor is to be given better resistance to mechanical stresses, the synthetic resin concrete must be sufficiently thick to be self-supporting, i.e. the minimum thickness must be 15- 20 mm. A thickness of 5 mm on a good, sound floor is normally sufficient and perfectly adequate.
The viscosity of the resins, pot life and hardener depend on the prevailing temperature. To make sure of thorough mixing, the resins and aggregates should not be colder than 15 C.
This temperature is also the lower limit of the curing temperature of non-accelerated binder systems. When lower curing temperatures are unavoidable, the hardener should be accelerated with some hardeners.
At a normal temperature the synthetic resin concrete cures completely within 24 - 28 hours, depending on the reactivity of the binder. Under these conditions the concrete is sufficiently strong to take minor mechanical stresses after only 12 hours. Full mechanical loading is possible after 3 - 7 days. The concrete should never be exposed to chemical attack in less than seven days.
Conditions are different with an amino polyimidazoline type hardener having low reactivity and long pot life with an amine value of 350-400 and AHEW 93, because it only acquires a measurable strength after a cure of more than 24 hours.
Slight mechanical stress may be applied after two to three days. Full mechanical and chemical service conditions can nevertheless also be applied after seven days because the system with containing such a hardener makes up for the initially retarded cure within the time that remains.
M. Namık Kayaalp
Kimya Mühendisi
Ecelak Boya Kimya Ltd. Şti.
Kaynakça
1 Schering Industrie-Chemikalien.
2. H.Lee, K.Neville handbook of Epoxy Resins.
3. Huntsman Advanced Materials (Switzerland) GmbH Klybeckstrasse 200 P.O. Box 4002 Basel Switzerland
4. Epoxy Polymers, Edited by Jean-Pierre Pascault and Roberto J. J. Williams, WILEY-VLH Verlag umbH.
5. Paint and Coating Testing Manual Fifteenth Edition of the Gardner-Sward Handbook, Joseph V. Koleske.