Öğütme Sisteminde Üretim Proseslerinin Optimizasyonu
1. Giriş
Uzmanlar, meslektaşlar ve müşterilerle yapılan görüşmelerde, boya, kaplama ve mürekkep endüstrisindeki öğütme ve dispersiyon işlemlerinin tasarımı için tesisin üretim kapasitesinin, örneğin yeni yatırımlar için belirleyici faktör olduğu görüşü tekrar tekrar dile getirilmektedir.
Karıştırıcı boncuk değirmenleri birçok ürün için kullanılmaktadır. Ufalama sonucunun esasen bir ürünün spesifik enerjisinin fonksiyonu olması nedeniyle, karıştırıcı boncuk öğütücüsüne mümkün olan en yüksek güç girişi çoğu durumda belirleyici çalışma parametresi olarak görülmektedir.
Güç yoğunluğundaki ve dolayısıyla değirmene giden güç girişindeki salt bir artışın, spesifik enerji gereksiniminde de bir artışa neden olduğu argümanı, ürünün fiyatına kıyasla daha yüksek enerji maliyetlerine sahip olmanın kabul edilebilir olduğu iddiasıyla sıklıkla reddedilir.
Aşağıdaki makalede, bir kalsiyum karbonatın ufalaması için basit bir örnek ilk olarak çeşitli parametrelerin güç girişi, spesifik enerji gereksinimi ve üretim kapasitesi üzerindeki etkisini göstermek için kullanılacaktır.
Daha sonra, denenmiş ve test edilmiş bir pinli öğütme sisteminin nasıl değiştirildiği ve daha yüksek üretim kapasitelerini kolaylaştırmak ve aynı zamanda verimliliği artırmak için boya, kaplama ve mürekkep endüstrisi için özel olarak ayarlanmış çalışma parametreleri izah edilecektir.
Saha testlerinin sonuçları, üretim kapasitesindeki potansiyel artışın tartışılması için kullanılacaktır.
2. Karıştırıcı boncuk değirmenlerinde ufalama sırasında çeşitli çalışma parametrelerinin üretim kapasitesi ve spesifik enerji ihtiyacı üzerindeki etkisi
Karıştırıcı boncuk değirmenlerinin ufalaması ve çalışma davranışı Stehr [1] ve Weit [2] tarafından derinlemesine araştırılmıştır. Ufalama davranışındaki kapsamlı bir faktörün spesifik enerji, yani öğütme ürününün (katı) kütlesi veya hacmine göre öğütme haznesine sağlanan enerji olduğu ortaya çıkmıştır (bkz. Denklem (1)).

Farklı boyutlarda öğütme ortamları ile yapılan araştırmalar, spesifik enerjiye ek olarak, öğütme boncuğu boyutunun, karıştırıcı boncuk frezelerinde ufalama üzerinde önemli bir etkiye sahip olduğunu göstermiştir (Joost [3], Schwedes [4], Thiel [5], Bunge [6], Mankosa ve ark. [7], Stadler ve ark .[8] ve Roelofsen [9].
Öğütme boncuklarının boyutunun ufalama görevine göre ayarlanması, belirli enerji gereksiniminde bir dereceye kadar önemli bir azalma sağlar.
Kireçtaşının süreksiz ufalaması için, Kwade [10] ayrıca karıştırıcının çevresel hızının ve öğütücü ortam yoğunluğunun spesifik enerji ve ürün inceliği arasındaki korelasyon üzerinde sistematik bir etkiye sahip olduğunu belirtmiştir.
Öğütme boncuklarının kinetik enerjisinin bir ifadesi olarak, Kwade [10] öğütme ortamı SEGM’sinin stres enerjisini öğütme ortamı yoğunluğunu GM, öğütme boncuğu çapı dMK ve karıştırıcının çevresel hızının bir fonksiyonu olarak tanımlamıştır (bkz. Denklem (2)).

Çalışma parametrelerinin, öğütme boncuğu yoğunluğunun, karıştırıcı diskinin çevresel hızının ve öğütme ortamı boyutunun etkisinin araştırılması sırasında, sabit spesifik enerji girişi ile, en büyük ürün inceliğinin elde edilebileceği optimal bir stres enerjisinin olduğunu
gösterebilmiştir.
Bu etkiler basit bir örnekle açıklığa kavuşturulmalıdır. Kalsiyum karbonat iki nedenden dolayı seçilmiştir:
1. Pigmentli sistemler için, uygun bir ürün kalitesi elde etmek için parlaklık, şeffaflık ve renk yoğunluğu gibi ek kalite özellikleri toplu olarak eşleşmesi gerektiğinden, partikül boyutu dağılımı aracılığıyla test sonuçlarının basit bir değerlendirmesi yeterli değildir.
2. Ek olarak, değişen yükleme koşulları, boyalar, kaplamalar ve mürekkepler için aynı ürün kalitesinin karakterizasyonu için formülasyonun da değiştirilmesi gerektiği anlamına gelebilir.
Bununla birlikte, bu örnekte tartışılan çalışma parametreleri arasındaki korelasyonlar niteliksel olarak herhangi bir malzeme sistemine taşınabilir. Bir optimumun belirlenmesi için en az üç test ayarı gereklidir.
Ufalamayı ilerletmek için gereken optimum stres enerjisi aralığına her zaman ulaşılamaz. Operasyonel güvenilirlik veya hedef ürün çıktısı ile ilgili olarak, çoğu durumda daha da küçük öğütme boncukları kullanmak pratik görünmemektedir.
Bu örnekte, ticari bir kireçtaşı başlangıçta sirkülasyon modunda aynı değirmende özdeş öğütme boncukları ile ve karıştırıcı milinin üç farklı çevresel hızı ile işlenmiştir: 7 m/s, 10.5 m/s ve 14 m/s. Her seferinde, numuneler 0.03 kWh/kgFS, 0.07 kWh/kgFS ve 0.1 kWh/
kgFS’lik spesifik enerji girişinden sonra bir Malvern MasterSizer 3000 ile analiz edilmiştir (aşağıdaki tabloya bakınız).

Testin sonuçları Şekil 1, d90 ‘ın spesifik enerji girişinin bir fonksiyonu olduğu’ de gösterilmiştir. Hedef değer olarak 6 μm’lik bir d90 tanımlandı.
Bu durum, kullanılan öğütme ortamı ile, karıştırıcı milinin en düşük çevresel hızı ve en düşük spesifik enerji tüketimi ile istenen hedef değere ulaşılabileceğini göstermektedir.
Ancak, bu ayarlarda çok düşük güç girişi nedeniyle, ortaya çıkan üretim kapasitesi de en düşük seviyededir (bkz. Şekil.4).
[caption id="attachment_143113" align="aligncenter" width="435"]

Şekil 1: Karıştırıcı milinin farklı çevresel hızları ile kireçtaşının ufalaması.[/caption]
Bu bulgu, yapılan testler için taşlama ortamının gerilim enerjilerini göz önünde bulundurulduğunda doğrulanır (bkz. Şekil 2). Şimdi hedef, en düşük enerji gereksinimi
ile en yüksek üretim kapasitesine ulaşmaktır.
Bu amaçla, karıştırıcı şaftının karıştırıcı uç hızı artırılır ve öğütme boncuğu etkisi başına aynı stres enerjisinin mevcut olduğu durumlarda öğütme ortamı boyutu hesaplanır (aşağıdaki basit hesaplamaya bakın).

Şimdi, 1,7 mm’den daha fazla çapa sahip 1,0 mm öğütme boncukları sabit taşlama ortamı yoğunluğu ve 14 m/s çevresel karıştırıcı şaft hızları ile kullanılırsa, ufalama sonuçları, spesifik enerjinin bir fonksiyonu olarak çizildiğinde karşılaştırılabilir (bkz. Şekil 3).
[caption id="attachment_143115" align="aligncenter" width="317"]

Şekil 2: Öğütme boncuklarının gerilim enerjisinin bir
fonksiyonu olarak ufalama sonuçları.[/caption]
[caption id="attachment_143116" align="aligncenter" width="304"]

Şekil 3: Kireçtaşının farklı çevresel karıştırıcı şaft
hızları ile ufalaması, öğütme boncuğu boyutunun ek
varyasyonu.[/caption]
Olası üretim oranları göz önüne alındığında, karıştırıcı milinin uç hızının ve dolayısıyla öğütme ortamının kinetik enerjisinin artması nedeniyle sadece güç girişinin arttırılmasıyla daha yüksek bir üretim kapasitesine ulaşılabileceği açıktır.
Bununla birlikte, bu yüksek üretim kapasitesi, artan spesifik enerji gereksinimi ile ilişkilidir.
Buna karşılık, öğütme boncuğu boyutunun eş zamanlı optimizasyonu ile, üretim kapasitesi, daha yüksek enerji girişlerine gerek kalmadan olağanüstü düzeyde arttırılabilir (bkz. Şekil 4).
3. Mevcut Pinli Öğütme Sisteminin Optimizasyonu
1991‘de patentli ZETA Pinli öğütme sistemi ile karşılaştırıldığında, NEOS öğütme sistemi ile birkaç önemli yükseltme yapılmıştır (bkz. Şekil 5):
• Öğütme haznesinin çift çeketindeki soğutma suyu akışı optimize edilmiştir. Buna ek olarak, yüksek aşınma direncine ve maksimum termal iletkenliğe sahip bir seramik malzeme artık öğütme haznesinin iç kısmı için standarttır.
• Karıştırıcı şaftı, bir yandan akışla ilgili optimizasyon nedeniyle, mevcut soğutma yüzeylerindeki ürün alışverişi iyileştirilecek şekilde tasarlanmıştır. Öte yandan rotor soğutması ilavesi için maksimum soğutma yüzeyinin mevcut olmasına dikkat edilmiştir.
Soğutma verimliliğindeki iyileşme, öğütme sisteminin yeni tasarımında önemli bir husustur,
çünkü çoğu durumda öğütme haznesine giden güç girişi öncelikle ürünün sıcaklık limitleri ile sınırlıdır.
• Öğütme haznesi hattı ile karıştırıcı şaftı üzerindeki pinler arasındaki boşluk azaltılmıştır. Sonuç olarak, aşırı küçük öğütme boncuklarının daha yoğun ivmelenmesi mümkündür. Bu, önemli ölçüde daha yüksek bir enerji yoğunluğuna ve dolayısıyla öğütme haznesine daha yüksek olası güç girişine yol açar.
Sonuç olarak, aynı öğütme boncuğu boyutu, öğütme ortamı yoğunluğu ve karıştırıcı mili hızı ile, bu öğütme boncuklarının daha yüksek bir ortalama kinetik enerjiye sahip olduğu anlamına gelir.
Ek olarak, bu, özellikle kesme inceltme ürünleri durumunda, makinede daha düşük viskoziteli bir ürüne yol açan ürün üzerinde daha yüksek kesme gerilmelerine neden olur.
• Öğütme ortamı elek sistemindeki ekranın çapı büyütülmüştür. Bu, eleğin ayırma alanını önemli ölçüde artırdı. Daha önce açıklanan viskozite etkisi ile birlikte, bu, elekteki öğütme boncuklarının ve kaba ürün parçalarının birikmesini daha verimli bi şekilde önler.
Bu yeni özellikler nedeniyle, çeşitli ürünlerin öğütülmesi veya dağıtılması sırasında önemli ölçüde daha yüksek ürün verim oranlarında daha küçük öğütme boncukları kullanmak mümkün olmuştur.
[caption id="attachment_143118" align="aligncenter" width="336"]

Şekil 5: NEOS öğütme sisteminin temel
gösterimi[/caption]
Aynı öğütme ortamı doldurma kütlesi ile, daha küçük öğütme ortamlarının kullanılması, öğütme boncuklarının sayısının ve dolayısıyla birim zaman başına temas veya stres sayısının katlanarak artması anlamına gelir.
Daha yüksek bir potansiyel ürün çıktısı, öğütme süresi başına sirkülasyon sayısında bir artışa ve böylece öğütme haznesindeki ürün parçacıklarının daha dar bir ikamet süresi dağılımına yol açar.
Öğütme odasından ürün beslemesinden ürün çıkışına bir geçiş sırasında ürünün daha kısa kalma süresi ve buna bağlı olarak daha düşük enerji girişi nedeniyle, öğütme devresinin soğutulmuş parti tankları ile donatılması koşuluyla, ürün sıcaklığının kontrolü kolaylaştırılır.
• Buna ek olarak, karıştırıcı şaft geometrisi, çok yüksek ürün verim oranları ile bile, öğütücü ortam ayırma sistemi alanında sıkıştırılmadan öğütücü ortamın dolaşımı iyileştirilecek şekilde değiştirilmiştir.
Bu, benzer kurulu motor gücü ve öğütme odası boyutları ile, daha yüksek bir üretim kapasitesinin elde edilebileceği anlamına gelmez. Daha küçük öğütme ortamı kullanma kabiliyeti ve daha yüksek ürün verim oranları nedeniyle, çeşitli ürünler için daha düşük bir enerji gereksinimi de eşlik eder.
Bu, öğütme ortamındaki aşınmanın azalmasına, makine bileşenleri üzerindeki stresin
azalmasına ve dolayısıyla üretilen ürün hacmine göre arıza sürelerinin, bakım ve yedek parça maliyetlerinin azalmasına neden olur.
4. Gerçek Müşteri Ürünü ile Saha Testlerinin Sonuçları
Siegwerk Druckfarben AG & Co. şirketi ile birlikte KgaA, çeşitli gerçek ürünlerle saha testleri gerçekleştirildi.
ZETA öğütme sisteminden NEOS öğütme sistemine geçilerek, güç girişindeki potansiyel artış birkaç kriterin bir fonksiyonu olmasına rağmen, tüm ürünler için %18 ile %143 arasında çok geniş bir aralıkta makinenin taşlama odasına güç girişini artırmak mümkün
olmuştur.
Burada önemli faktörler, makinenin kurulu motor gücüne ek olarak, sıcaklık sınırı, viskozite ve ürünün reolojik davranışıdır. ZETA öğütme sistemi ile, kesme inceltici ürünlerin viskozitesine bağlı olarak, çeşitli ürünler için makinenin güç sınırına ulaşmak çoğu zaman mümkün olmamıştır.
Buna karşılık, NEOS öğütme sistemi ile, ürünün sıcaklık sınırına ulaşmadan değirmenin güç sınırına ulaşmak her zaman mümkün olmuştur. (bkz. Şekil 6)
Bu, elbette bir yandan makinenin soğutma kapasitesi ile açıklanabilir, ancak diğer yandan daha önce tartışılan viskozite etkisi ile de açıklanabilir. Daha yüksek kesme stresi ve bunun sonucunda değirmende ürünün daha düşük viskozitesi nedeniyle, öğütme odası duvarının
yakınında ve karıştırıcı şaftının yakınında daha iyi bir ürün değişimi vardır, bu da öğütme odasından daha iyi ısı dağılımı ile sonuçlanır.
[caption id="attachment_143119" align="aligncenter" width="438"]
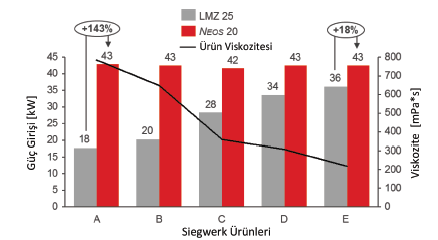
Şekil 6: ZETA 25‘ten (LMZ 25) NEOS 20’ye geçişle elde edilen Performans
Artışı çeşitli müşteri ürünleri için öğütme sistemi [11][/caption]Bununla birlikte, Schönstedt [12] özellikle ürüne bağlı olarak formülasyonun değiştirilmesinin de gerekli olabileceğini göstermiştir. Kullanılan değirmen teknolojisine
bağlı olarak, örneğin ürün viskozitesinde, renk yoğunluğunda, şeffaflıkta veya parlaklıkta değişiklikler meydana gelebilir.
Bu nedenle, standardın spesifikasyonlarına ulaşmak için, en basit durumda çözücünün
konsantrasyonunu değiştirmek gerekir. Bununla birlikte, bazı durumlarda, yalnızca bağlayıcı etkin maddenin değiştirilmesi istenen sonucu vermiştir.
5. Özet
Saha testleri, yeni bir öğütme sisteminin kullanılmasıyla, güç girişinde çeşitli artışlar olduğunu ve böylece üretim kapasitesinin elde edilebileceğini göstermiştir. Değirmenin çalışma parametrelerinin değiştirilmesi ve/ veya ürünün formülasyonu ile birleştirildiğinde, spesifik enerji gereksinimi, sabit ürün kalitesi ile bile bir dereceye kadar önemli ölçüde azaltılabilir.
Burada, önemli çalışma parametreleri öncelikle öğütme ortamı boyutu ve değirmen boyunca ürün çıktısıdır. Üretim kapasitesinde sağlanabilecek artış için belirleyici faktörler ağırlıklı olarak viskozite, reolojik davranış ve sıcaklık limitleri gibi ürün özellikleridir.
Ayrıca, çalışma parametrelerinin optimizasyonu veya değirmendeki güç yoğunluğunun artması nedeniyle ürün üzerindeki yükleme koşulları değiştirildiğinde formülasyonun kısmi olarak ayarlanması gerektiği gösterilmiştir.
Kaynakça
[1] N. Stehr, Zerkleinerung und Materialtransport in einer, Rührwerkskugelmühle. Tez, TU Braunschweig, 1982
[2] H. Weit Betriebsverhalten und Maßstabsvergrößerung von Rührwerkskugelmühlen. Tez, TU Braunschweig, 1987
[3] B. Joost, A. Kwade Feinstzerkleinerung, Rührwerksmühlen. Das Keramiker - Jahrbuch 1996, s. 23 -38
[4] J. Schwedes, A.Kwade, H. - H. Stender, Hochschulkurs Zerkleinern und Dispergieren mit Rührwerkskugelmühlen Umdruck zum Hochschulkurs vom Institut für Mechanische Verfahrenstechnik und Kwade + Schwedes Zerkleinerungstechnik, Braunschweig, 2008
[5] J. P. Thiel, Energiebedarf und Durchsatzverhalten der Kohlenasszerkleinerung in einer Rührwerkskugelmühle. Tez, TU Braunschweig, 1993
[6] F. Bunge, Mechanischer Zellaufschluß in Rühr¬werkskugelmühlen. Dissertation, TU Braunschweig, 1992
[7] MJ Mankosa, G. T. Adel, RH Yoon, Effect of media size in stirred ball mill grinding of coal. Toz
Teknolojisi 49, 1986, S. 75 -82
[8] R. Stadler, R. Polke Chemie, J. Schwedes, F. Vock, Naßmahlung, Rührwerkskugelmühlen.- Engenieur - Technik, 62, 907 -915, 1990
[9] D. P., Roelofsen Entwicklungen auf dem Gebiet des Pigmentdispergierens mit Rührwerkskugelmühlen. Farbe + Eksiklik 97, 1991, 3, S. 235 -242
[10] A. Kwade, Autogenzerkleinerung von Kalkstein, Rührwerkmühlen. Tez, TU Braunschweig, 1996, ISBN 3 -8265 -2082 -3
[11] H. - H. Stender, NETZSCH ile ambalaj mürekkebi üretiminin ilk endüstri test sonuçları Neos teknolojisi, sunum, Dispersiyon Günleri, 15 -17 Mayıs 2017, Selb
[12] B. Schönstedt, Yeni boncuk değirmeni teknolojisinin düzenli üretime uygulanması, sunum, Dispersiyon Günleri, 15 -17 Mayıs 2017, Selb
Dr. Stefan Mende Büşra Örs
Teknik ve Bilimsel İletişim Müdürü
NETZSCH
Büşra Örs
Teknik Satış Mühendisi
NETZSCH