1. Influence of Galvanizing on the Base Material
In principle, constructions and components are exposed to stresses in which the mechanical properties of the base material are stressed. This also applies to parts which have been subjected to electrolytic galvanizing due to corrosion protection.
It was therefore on a possible influence of electroplating on the mechanical properties of the base material engaged.
According to various investigations, the influence of zinc layers subjected to zinc electroplating in the area of tensile strength, i.e. under rapid stress, is very small and rather lower than for other metals deposited as a result of the electroplating process (deformation-inhibiting chromium excepted).
Even internal stresses in the actual zinc layer apparently remain without influence on the base material. When electroplating in acidic electrolytes, properties from the area of dynamic stress such as fatigue strength and structural strength are almost unaffected.
In addition to that, it’s different when electroplating in alkaline electrolytes with low current efficiency and high hydrogen evolution. As a result of this, a more or less strong hydrogen charging takes place, which can lead to hydrogen embrittlement, depending on the characters of the base material.
For example, in bending tests with galvanized spring steel samples, it was found that the base material acts significantly worse when the zinc layer is deposited from an alkaline electrolyte.
While the bending coefficient and the number of bends to break with increasing zinc layer thickness hardly change when the layers are of acidic electrolyte, it drops drastically when an alkaline electrolyte is used (see Figure 1).
These and numerous other examinations carried out show that the main influence of electroplating is due to the charging with hydrogen and the resulting hydrogen embrittlement.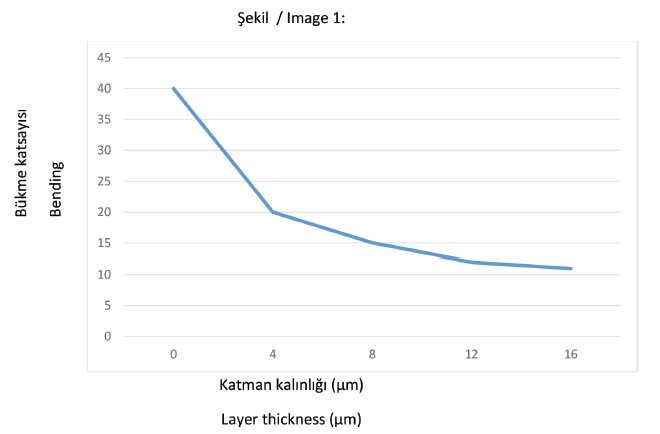
Hydrogen absorption is often the cause of these brittle fractures in the material. They can be very dangerous for the material or component behaviour, because they usually occur in a crack without a simultaneous macroscopic shape change.
Especially, they do not arise immediately, but only after a long period of operation without prior notice. For these reasons, the terms hydrogen-induced crack formation or cathodic stress corrosion cracking are used in part especially in the scientific literature, instead of the term hydrogen embrittlement.
This problem has become particularly acute in recent times in that attempts are being made to exploit the strength of steel achievable by heat treatment more and increasingly to use unalloyed or poorly alloyed high-strength steels.
Thus, the material loses its toughness and becomes particularly sensitive to the diffusion of hydrogen.
2. Hydrogen Embrittlement as a System Property
Embrittlement of a material is defined as a state of low ductility in which even a relatively small absorption of mechanical energy can cause irreversible destruction. If it occurs as a result of the ingress of hydrogen into the material, it is called hydrogen embrittlement.
By absorbing hydrogen under certain conditions, the elastic properties of the base material are strongly influenced so that it becomes brittle and does not have sufficient resistance to a gradually acting mechanical load.
While the behaviour against a sudden stress such as impact or tensile impact changes only slightly, a strong influence in the plastic field is observed.
Characteristics such as tensile strength, notch impact strength and the like are thus generally not impaired, but the ductility, yield strength, elongation, constriction, bending strength, etc.
As already stated, this result can be a so-called brittle fracture, it represents a kind of material separation that is very dangerous and usually occurs without warning.
The influence of hydrogen on the base material or component depends on three conditions: there must be sufficient supply of hydrogen, sufficient hydrogen charge of the base material and, finally, suitable conditions must be present in the material or component which allows the mechanical properties of the hydrogen to be influenced.
All factors and parameters can affect each other both positively and negatively. Therefore, hydrogen embrittlement usually depends not only on one but on several influencing factors and can be attributed to various causes. Thus, it has the character of a system property.
2.1 Hydrogen Supply in Electroplating
In galvanic surface treatment, hydrogen can penetrate into the material or into the base material substantially in three process steps:
•In pickling,
•In cathodic pre-treatment and
•In electrolytic metal deposition.
It can be safely assumed that the predominant part of the hydrogen penetrating into the material does not originate from the electrodeposition but from the pre-treatment.
According to the widespread opinion that hydrogen embrittlement is arising from the process of zinc deposition (and also from other galvanic layered metals) is not true in the vast majority of cases.
Pickling is known as an electrochemical reaction in which anodization of the material takes place at the anodic sites by resulting in the reduction of hydrogen ions and the formation of hydrogen atoms at the cathodic sites.
This process takes place on the cathode surfaces also in the electrolytic degreasing and the electrodeposition of metal, but then only when the electricity yield is less than 100%.
The hydrogen atoms are first adsorbed on the component surface and then (depending on conditions faster or slower) recombine to hydrogen molecules, which escape as hydrogen in gas form.
These processes can be described as follows: Hydrogen ions (protons H+) are usually bound to water and have the form of hydronium ions (H3O+). The hydronium ions are freed from the hydrate shell at the phase boundary material / liquid, discharged by reduction (electron uptake) and adsorbed on the metal surface:
H3O+ → H2O + H+
H+ + e- → Had
Each two adsorbed hydrogen atoms can recombine at the material surface to form a hydrogen molecule:
Had + Had → H2,ad
The adsorbed hydrogen H2,ad is desorbed and diffuses into the solution or escapes as hydrogen in gas form. Hydrogen is thus supplied to the metal surface both in atomic and in molecular form.
2.2 Mechanism of Hydrogen Diffusion in Zinc Plating
For diffusion of the hydrogen in the material surface, it is necessary to be present in atomic form. Due to their small diameter, the hydrogen atoms penetrate the material, occupying sites of lattice defects, grain boundaries, and microcracks, but may also pass through crystals (depending on the conditions present).
Hydrogen-influenced surface layers are formed, which can reach a depth of 30 μm. Molecular hydrogen is not diffusible. Only if the surface is highly porous, has larger cracks or cavities, hydrogen can penetrate even in the molecular state.
However, at the high hydrogen concentration prevailing at the phase boundaries, conditions may also occur under which the hydrogen molecules dissociate again and then diffuse in atomic form. Except in the appropriate form, hydrogen must also be in direct contact with the surface of the base material.
It must be at least partially occupied with hydrogen, so that diffusion can take place. In electrolytic electroplating, however, the absorbable hydrogen produced at the phase boundary is distributed between the base material and the zinc layer.
However, the properties of the base material can only influence the proportion that diffuses in the surface. How large this proportion is depends on both the electrolyte and the electrolysis conditions as well as the base material.
2.2.1 Influence of Electrolysis Conditions
During the electroplating process, hydrogen is precipitated simultaneously with zinc, starting from certain active sites, finally forms a compact zinc layer over the entire surface.
The adsorption of the hydrogen atoms therefore takes place first at the phase boundary base material / electrolyte and later to an increasing extent at the phase boundary zinc layer / electrolyte. The more zinc that separates, the greater the hydrogen overpotential.
Finally, when the entire surface is covered with a coherent layer of zinc, it forms a barrier to the further diffusion of hydrogen into the base material. In general, this is the case resulting a layer of 0.5 to 1 μm.
A 2 μm thick layer thus already forms a good diffusion barrier against hydrogen. The time until the formation of such a layer is required is critical for the diffusion of hydrogen into the base material and thus also for the hydrogen embrittlement. Their length is different for the different zinc electrolytes and as follows:
•for a high-cyanide electrolyte 56 mAs / cm²,
•for an alkaline cyanide-free electrolyte 18 mAs / cm² and
•for a weak acid electrolyte 6.7 mAs / cm².
After this layer is created, hydrogen diffusion no longer takes place in the base material. The electricity yield of the electrolyte also has no influence on the hydrogen charge. The hydrogen is essentially absorbed only in the zinc layer.
Due to the different hydrogen absorption, two mechanisms become prominent. For the Canadian baths with no brightener, the pore mechanism essentially applies, for glitter-containing so-called absorption-diffusion mechanism.
The mechanisms differ in that the source of the diffusing hydrogen is different. In the pore mechanism, the hydrogen is relevant, which is absorbed at the beginning of the deposition on still uncovered points of the base material.
In the absorption diffusion mechanism, on the other hand, the one which is absorbed in the zinc layer and penetrates into the base material from there.
The second process is the slower, the less hydrogen is absorbed in the zinc layer and the lower the gradient of the hydrogen concentration, thus, the subsequent zinc layer should preferably not contain more hydrogen compared to the previous one.
Therefore, the rate of hydrogen absorption in steel and its changes in the course of the deposition depend essentially on the parameters of the layer formation and less on the coated steel.
As a rule, the faster the zinc is deposited and forms a coherent layer, the lower the risk of hydrogen charging. It is therefore convenient to work with high current densities.
2.2.2 Influence of the Base Material
The tendency of unalloyed or poorly alloyed high-strength steels to absorb hydrogen has already been mentioned. Apart from that, steels with a carbon content > 0.5% should be more sensitive to hydrogen charging. Opinions differ about the influence of the alloy components chromium, tungsten and nickel.
In terms of surface condition, microcracks, micropores, cavities and other irregularities promote hydrogen penetration. These can be seen, for example, if the material has been severely deformed before electroplating or if the surface has been roughened or damaged by mechanical grinding or polishing.
A chemically or electrochemically brightened surface absorbs only 30 to 40% of the hydrogen compared to a mechanically treated surface. However, rough surfaces may also reduce the tendency for hydrogen charging when hydrogen atoms in rough sites preferentially recombine into molecules.
The diffusion of hydrogen is favoured when surface contaminants contain so-called contact poisons such as carbon, phosphorus, lead or tin. They probably lower the hydrogen over-potential and slow down the growth of the zinc layer.
The structure has an important influence. Hydrogen charging of the base material is particularly high when it is braced or distorted.
This can be done for example by a pre-cold working or heat treatment (hardening, case hardening). Hydrogen can be incorporated into the lattice in such cases and then, when it escapes again at room or higher temperature, lead to a lattice contraction.
The theories about the behaviour of hydrogen in microstructural anomalies differ widely.
3. Preventing Hydrogen Embrittlement
Hydrogen embrittlement is a system property. If it is wanted to be prevented, measures must be taken in all areas that affect them, so that both in the material and the component and in the galvanic surface treatment. In general, the material and component side measures have to be preferred.
It can be often prevented that the critical hydrogen charging only after the last process in the chain of manufacturing technologies, which means the surface treatment occurs and the error is therefore only then found. In such critical cases, measures have to be taken in the surface treatment all possible from the electroplating side.
In practice, hydrogen embrittlement must be expected when hardened parts, tempered screws, springs and parts made of high-strength steels or those produced by cold-cutting, cold-rolling or pulling are present.
Regarding the technically important unalloyed carbon steels and the low-alloyed tempered steels, the tensile strength of 1200 N/mm² is to be regarded as critical; beyond which the measures described below should be carried out. Materials made of titanium are also among the materials susceptible to hydrogen embrittlement.
The effectiveness of such measures can be determined according to DIN 50969 or by a defined slow test.
3.1 Measures for Galvanic Surface Treatment
Measures in the process of galvanic surface treatment are possible or necessary in pre-treatment as well as in electrodeposition and post-treatment.
3.1.1 Pre-treatment Measures
•For all pre-treatment procedures, exposure times should be used as short as possible.
•Pickling only with the addition of such inhibitors that do not simultaneously inhibit the recombination of hydrogen atoms to H2 molecules.
In the case of particularly vulnerable parts, pickling can take place in a protective gas atmosphere. If hydrogen loading during pickling is inevitable, it may be necessary to intermediate temper (usually 0.5 hours at 150°C).
•In the case of high-strength parts, in particular for safety parts, only mechanical methods for cleaning and activating have to be used, for example blasting (in the case of particularly endangered parts in aviation, for example, by blasting with a defined aluminium oxide as blasting medium.
•Electrolytically only anodically degrease.
3.1.2 Measures for Actual Electroplating
•Choose a well-covering electrolyte to quickly reach the minimum barrier layer thickness of 0.5 μm, which prevents hydrogen from diffusing. As a rule, an acidic electrolyte is suitable.
•Use electrolytes with as much as possible 100% electricity yield under such conditions that they are actually achieved in a concrete application.
•Perform the electroplating process with pulsating direct current. By choosing appropriate parameters, crystallization conditions can be achieved that lead to fine-grained and low-stress layers.
3.1.3 Post-treatment by Annealing
•Post-treatment by tempering, irrespective of which process step it is carried out, is best carried out immediately, at the latest 24 hours thereafter. Most of the hydrogen contains the first 0.1 to 0.2 μm of the zinc layer.
Therefore, if it’s annealed immediately after galvanizing, it’d be possible to have the possibility that the hydrogen enriched at the phase boundary does not diffuse into the base material but through the zinc layer.
However, this must not be too thick and not come from a polishing bath. If a longer time elapses until tempering, not only the hydrogen from the phase boundary, but under certain circumstances also that from the bright zinc coating can diffuse into the base material.
•The heating up to the desired temperature is to be carried out gradually in order to avoid damage to the base material and zinc layer due to too rapidly diffusing hydrogen.
•If it’s possible that hydrogen can escape (thin, additive-free zinc layer), it is generally sufficient for 2 to 3 hours aging at 140 to 200°C, which may also be carried out in an oil bath. At higher degrees of deformation of the components longer holding times may be necessary.
•For high-strength steels and constructions with high stresses, for example by work hardening, the highest temperature limited by the tempering temperature and the material condition as well as the duration of tempering must not be exceeded. Guide values are given in Table 1.
* The heat treatment should be done immediately after electroplating.
İzzet Aydın
General Manager
Hillebrand Chemicals Kimyasal Pazarlama Ltd. Şti.
References:
Metalloberfläche, Paatsch W.
DIN 50969.
Metalloberfläche, Tolls E.
Materials Performance, Isecke B.
Zasc. met., Schitanow W.J.
Korr. und Metallschutz, Fischer H.