Kuru İnce ve Çok İnce Öğütmede Kullanılan Karıştırmalı Bilyalı Değirmenler
Öğütme, madencilik, cevher işleme, çimento vb. dâhil olmak üzere farklı endüstrilerdeki ufalama prosesinin temel adımlarından birisidir. Genellikle cevher prosesinde mineralleri serbestleştirmek, ayırmak ve mikronize etmek için proses akış şemasında kullanılır.
Geleneksel öğütme tipik olarak tamburlu (aktarılan ortam, yatay) değirmenler tarafından gerçekleştirilir. Bunlar nispeten kaba (iri) öğütmeye uygun çubuklu değirmenler ve pratik olarak daha ince boyutlara kadar öğütme kapasitesine sahip bilyalı değirmenler olabilmektedir.
Her iki tipte de, değirmen döndükçe kaldırılan ve düşürülen, darbe (impact) ve aşındırma (attrition) kuvvetleriyle şarjı (öğütülecek malzemeyi) daha ince tane boyutlarına öğüten, çubuk veya bilye şeklindeki öğütücü ortamı içeren döner bir tambur kullanılmaktadır. Bilyalı değirmenlerle geleneksel öğütme, parçacıkları yaklaşık 100 mikrona kadar ufalayabilmektedir.
Ekonomik olması durumunda, bilyalı değirmenler veya karıştırma ortamlı değirmenler kullanılarak daha sonra ince ve çok ince öğütme yapılır. İnce ve çok ince öğütmenin tanımı değişmekle birlikte ince öğütmenin genellikle 100 mikronluk P80 değerlerinin (parçacıkların
ağırlıkça %80’inin altına geçtiği elek boyutu) ve çok ince öğütmenin (fine grinding) 20 mikronluk P80 değerlerinin altında gerçekleştiği kabul edilir.
Çok ince öğütmede (ultra fine grinding) kullanılan değirmenler önceleri ilaç, boya, kil, boya ve pigment üretimi de dahil olmak üzere çok sayıda endüstride kullanılıyorken, günümüzde maden sektöründe, bu değirmenler büyük ölçüde altın cevheri, manyetit cevheri, bakır-kurşunçinko yatakları ve tane serbestleşme boyutları 15 mikron veya daha küçük olan platin cevheri parçacıklarını serbestleştirmek için kullanılmaya başlanmıştır.
Bilyalı değirmenler geleneksel olarak minerallerin ince öğütülmesi için kullanılır ve bu durumlarda, temas alanını arttırmak ve çarpışma yoğunluğunu azaltmak için geleneksel öğütmedekinden daha küçük bilya boyutları seçilir ve daha düşük değirmen hızları
kullanılır. Ancak bu değirmenlerin 75 mikronun altında öğütme yapıldığında verimliliği düşer ve 30 mikron civarında nadiren ekonomik olur.
Karıştırmalı ortam değirmenler, ince ve çok ince öğütme için giderek artan bir şekilde bilyalı değirmenlerin yerini almakta; tipik olarak aynı ürün boyutuna öğütme sırasında bilyalı
değirmenlere kıyasla yaklaşık %30-40 daha az güç tüketimine imkân sağlamaktadır.
Karıştırmalı değirmende özgül enerji tüketiminin, geleneksel tamburlu değirmenle karşılaştırıldığında çok ince parçacıkların üretilmesi için daha az olduğu bilinmektedir.
Geleneksel öğütmeyle karşılaştırıldığında, karıştırmalı değirmenler daha az malzeme kaybına sahiptir; oksitlenme olmadığından, daha iyi bir ısı aktarımı ve toksik salınımın daha kolay işlenmesi nedeniyle hava temizleme cihazlarına ihtiyaç yoktur.
Daha ince öğütme elde etmek için kapalı devreli ve daha küçük öğütücü ortamlı tamburlu değirmenler kullanılabilmekte, ancak kinetik enerji üzerindeki etkilerinden dolayı bu
seçenek kısıtlanmaktadır. Öğütücü ortam boyutunun azalmasıyla kinetik enerjiye olan etki azalmakta, parçacık ve öğütücü ortam (bilya) teması sırasında enerji aktarımı azalmaktadır.
Bu kısıtlamalar, dönen karıştırıcılara ve sabit değirmen haznesine sahip çok ince
öğütme değirmenleri tarafından yerine getirilmektedir. Daha ince ürünlere sahip oldukları için de daha geniş bir yüzey alanına etki ederler. Ayrıca, çok ince öğütmede kullanılan öğütücü ortam (bilya) boyutu (2–3 mm), geleneksel öğütücününkinden (12–100 mm)
çok daha küçüktür.
Neden Kuru Öğütme?
Karıştırmalı ortamlı değirmenler tipik olarak ıslak (yaş) bir işlem olarak çalışır, çünkü su karıştırmayı teşvik eder ve yeniden topaklanmayı baskılamak için ürün parçacıklarını dağıtır. Kuru öğütmede, yeniden topaklanma, daha düşük yüzey enerjisine öğütme yardımcılarının
(grinding aids) eklenmesiyle bir miktar azaltılabilir, ancak bununla bile, yaş öğütmeye kıyasla çok daha yüksek bir pratik öğütme sınırına yol açar ve sonuçta önemli verim düşüşlerine neden olur.
Ancak bazı durumlarda kuru öğütme gerekli olabilir. Kuru öğütme, bazen öğütme verimliliğindeki bozulmayı dengeleyebilen kurutma veya atık su arıtma maliyetini ortadan
kaldırır ve aslında su temininin zor olduğu kurak bölgelerde gerekli olabilir. Kuru öğütme kimyasal nedenlerden dolayı da tercih edilebilir; örneğin, karıştırmalı ortam değirmenler, özellikle özel ince çimentolar için, çimento klinkerinin verimli bir şekilde öğütülmesinde
öne çıkmaktadır. Yine, boya ve plastik gibi sektörler için dolgu minerallerinin (mineral fillers) hazırlanmasında kuru öğütme yaygın olarak kullanılmaktadır.
Yaş öğütmeyle karşılaştırıldığında kuru öğütme çok daha az orta düzeyde aşınma gösterir. Aynı boyut dağılımı için kuru öğütme, değirmenin türüne bakılmaksızın yaş öğütmeye göre %15-50 daha fazla enerji gerektirir. Yaş öğütme, kuru öğütmeyle aynı enerji seviyesinde
daha ince parçacıklar üretebilir. Ancak, yaş öğütmenin ardından parçacık boyutu dağılımı, kuru ortamda olduğundan çok daha kısıtlıdır.
Aynı mineral için sonraki prosesin pülpünde Fe içeriği, kuru öğütmeyi takiben önemli ölçüde daha düşüktür çünkü bu, yaş öğütmeye göre belirgin şekilde daha az ortam ve daha az astar aşınmasıyla ilişkilidir.
Karıştırmalı Ortam Değirmenler
İnce ve çok ince parçacıkların verimli bir şekilde öğütülmesi, yüzey alanını ve bunun sonucunda ortaya çıkan çarpışma sıklığını artırmak için küçük öğütücü ortamlar gerektirir, ancak bilyalı değirmenler, pratik bir alt sınır belirleyen yerçekimi kuvveti tarafından bu tür küçük bilyalara uygulanabilen momentum bakımından temel olarak sınırlıdır.
Karıştırmalı ortamlı değirmenler, bir şaft ile ortama momentum uygulayarak bu sınırlamanın üstesinden gelir; bu, milimetre ölçeğinde küçük öğütücü ortamların kullanımına olanak tanırken, yine de şaft (karıştırma) hızına bağlı olarak –ve isteğe bağlı olarak- yüksek çarpışma yoğunlukları uygulayabilmektedir.
Karıştırmalı değirmenler 40 ila 300 kW/m3 arasında yüksek güç yoğunluklarına sahip olabilir (bilyalı değirmen için yaklaşık 20kW/m3 ile karşılaştırıldığında) belirli bir üretim hacminde tesis yerleşim alanı ihtiyacını da önemli ölçüde azaltabilir.
Ufalama için öğütücü hazne ve öğütme ortamı (çakıl, kum, bilya) kullanmanın ilk örneği, 1922’de Szegvari’nin bir kükürt süspansiyonunu hızla dağıtmak için çakıllarla dolu bir hazneyi karıştırmasıydı. Bu, 1928’de Klein ve Szegvari tarafından ilk ‘karıştırmalı bilyalı değirmen’ olarak geliştirildi.
Bu prototip, 1946’dan bu yana Union Process tarafından çeşitli formlarda üretilen, düşük karıştırma hızlı (3–5 m/s) dikey pinli bir değirmen olan Attritor değirmenine dönüştürüldü. Sonraki yıllarda, madencilik endüstrisinde kullanılan en yaygın türlerin aşağıda tanıtıldığı
birkaç başka karıştırmalı ortamlı değirmen tasarımı geliştirilmiştir.
Yerçekiminden Yararlanılan Karıştırmalı Değirmen Bu değirmenlerde ortam hareketi bir şaftın dönüşüyle sağlanır; hız, öğütücü ortamı tamamen askıya almak için yeterli değildir ve bu nedenle şaftın tepesinde, ortam, yerçekimi altında aşağıya doğru basamaklanır; Bu çökelme, verimli öğütme için ortamın yakın temas halinde kalmasını sağlar ve eleklere ihtiyaç duymadan ürün olarak çıkarılabilen ortamın üzerinde yerleşik bir yük bölgesine yol açar.
Çökmeyi sağlamak için öğütücü ortam nispeten büyüktür; çapları tipik olarak en az 12 mm’den birkaç cm’ye kadardır. Yer çekimi (gravite) esaslı ilk karıştırmalı değirmen, 1950’lerde Japan Tower Mill Company tarafından geliştirilen Tower Mill’di (3 m/s) ve 1980’lerde Metso, bu teknolojinin bir uyarlaması olan Vertimill’i geliştirdi. İlk kullanımlar,
nötralizasyon amacıyla kullanılan kireçtaşının yaş öğütülmesini içeriyordu ve 1980’ler ve 1990’larda, madencilik endüstrisinde yerçekimi esaslı karıştırmalı değirmenler benimsendi.
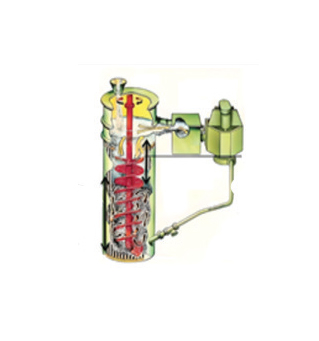
Karıştırmalı Ortam Detritoru (SMD), “dikey” bir sekizgen tanktan ve öğütücü ortamı akışkanlaştıran (bilya çapları tipik olarak birkaç milimetre mertebesinde) yüksek hızlı (11 m/s), çok katmanlı bir pimli şafttan oluşur. Bu değirmen attritor değirmenine benzer, ancak aslında 1948’de Du Pont tarafından pigment öğütme için icat edilen ve öğütme ortamı olarak Ottawa kumunu kullanan yüksek hızlı kum öğütücüden ibarettir.
1960’larda İngiliz China Clay (şimdi Imerys), başlangıçta ortam olarak kum kullanan SMD’yi geliştirdi, ancak son yıllarda kumun yerini küçük seramik (alümina) bilyaları aldı. Son 45
yıldır, SMD’ler özellikle kaolin ve kalsiyum karbonat öğütme uygulamalarında kullanılmakta, 1-2 mikron ürün boyutuna kadar parçacık üretmektedir. Günümüzde Metso bu değirmenleri metalik cevherlerin çok ince öğütülmesinde kullanılmak üzere de imal etmektedir.
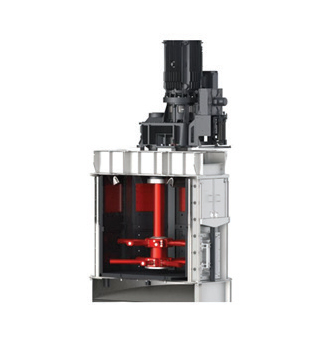
IsaMill–Mount Isa Mines Ltd. ve Netzsch tarafından geliştirilen ve 1999 yılında cevherin çok ince öğütülmesi için ticarileştirilen “yatay” bir diskli değirmendir. Karıştırıcının merkezi bir mile bağlı bir dizi delikli disk olduğu yatay silindirik bir öğütme haznesinden oluşur.
SMD’de olduğu gibi, yüksek hızlı ‘akışkan’ bir değirmen olarak kabul edilir ve çok ince ürün boyutları elde etmek mümkündür; 7 mikrona kadar düşük P80 değerleri pratiktir, nispeten ince öğütücü ortam bilya (4-8 mm) tarafından mümkün kılınır. IsaMill’ler, benzer çalışma koşulları (karıştırma hızları ve öğütücü ortam çapları) göz önüne alındığında SMD’lere benzer çok ince öğütme verimliliklerine sahiptir.
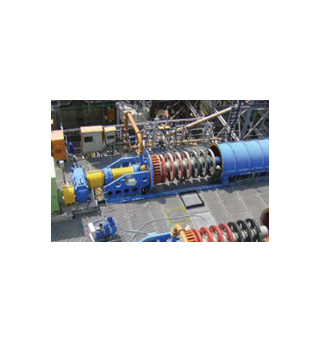
Kaynaklar
1. A.Gupta, D.S. Yan, Stirred mills-ultrafine grinding, A. Gupta, D.S. Yan (Eds.), Mineral
Processing Design and Operations: An Introduction (Second Edition), Elsevier (2016).
2. A.Jankovic, Variables affecting the fine grinding of minerals using stirred mills, Miner.
Eng., 16 (2003), pp. 337-345.
3. A.Jankovic, W.Valery, E. Davis, Cement grinding optimization, Miner. Eng., 17 (2004),
pp. 1075-1081.
4. A.Kwade, J. Schwedes, Chapter 6-Wet grinding in stirred media mills, A.D. Salman, M.
Ghadiri, M.J. Hounslow (Eds.), Handbook of Powder Technology: Volume 12 – Particle
Breakage, Elsevier BV (2007).
5. Á.Rácz, K.Bohács, F.Kristály, É.Gregus, G.Mucsi, Comparison of wet and dry stirred
media milling from energetic and mechanochemical point of view, XXIX International
Mineral Processing Congress, Moscow, Russia, 15-21st September (2018).
6. A.Szegvari, M. Yang, Union Process Inc., Attritor Grinding and Dispersing Equipment,
Available online at: https://unionprocess.com/tech_papers/Attritor_-Grinding-and-
Dispersing-Equipment.pdf (2019).
7. A.G.Doll, Fine Grinding, a Refresher, 49th Annual Canadian Mineral Processors Operators
Conference, Ottawa, Canada (2017).
8. A.K.Chatterjee, Cement Production Technology: Principles and Practice (1st Edition),
CRC Press (2018).
9. B.A.Wills, J.A.Finch, Chapter 7-Grinding mills, B.A. Wills, J.A. Finch (Eds.),
Wills’Mineral Processing Technology (Eighth Edition)-An Introduction to the Practical
Aspects of Ore Treatment and Mineral Recovery, Butterworth-Heinemann (2016).
10. B.D.Burford, E. Niva, Comparing energy efficiency in grinding mills, Metallurgical
Plant Design and Operating Strategies (MetPlant 2008), Perth, Australia, 18–19 August
(2008).
11. Chapter 10. Stirred mills—Ultrafine grinding. In Mineral Processing Design and Operations,
2nd ed.; Gupta, A.; Yan, D. (Eds.) Elsevier: Amsterdam, The Netherlands, 2016;
pp. 287–316.
12. G.Mucsi, A review on mechanical activation and mechanical alloying in stirred media
mill, Chem. Eng. Res. Des., 148 (2019), pp. 460-474.
13. H.Cho, J.Kwon, K.Kim, M.Mun, Optimum choice of the make-up ball sizes for maximum
throughput in tumbling ball mills, Powder Technol., 246 (2013), pp. 625-634.
14. H.de Bakker, Energy use of fine grinding in mineral processing, Metall. Mater. Trans.
E, 1E (2014), pp. 8-19.
15. L. Taylor, D. Skuse, S. Blackburn, R. Greenwood, Stirred media mills in the mining industry:
Material grindability, energy-size relationships, and operating conditions, Powder
Technology, Volume 369, 2020, 1-16.
16. M.R.Pryor, Chapter 7: Dry grinding, M.R. Pryor (Ed.), Mineral Processing (Third Edition),
Springer Science & Business Media (2012).
17. O.Altun, H.Benzer, A.Toprak, U.Enderle, Utilization of grinding aids in dry horizontal
stirred milling, Powder Technol., 286 (2015), pp. 610-615.
18. S.C.Chelgani, M.Parian, P.S.Parapari, Y.Ghorbani, J.Rosenkranz, A comparative study
on the effects of dry and wet grinding on mineral flotation separation – a review, J. Mater.
Res. Technol., 8 (5) (2019), pp. 5004-5011.
19. T.Yokoyama, Y.Inoue, Chapter 10-Selection of fine grinding mills, A.D. Salman, M.
Ghadiri, M.J. Hounslow (Eds.), Handbook of Powder Technology (Volume 12), Elsevier
Science B.V. (2007).
20. Union Process, The Evolution of Milling Technology [brochure], Available online at
https://unionprocess.com/pdfs/up-corporate-brochure.pdf (2012).
Prof. Dr. Öner Yusuf Toraman
Niğde Ömer Halisdemir Üniversitesi
Maden Mühendisliği Bölümü