MACBETH (Membranes and Catalyst Beyond Economic and Technological Hurdles)
In the process industry, the operations that need the greatest energy and resource consumption are the downstream processes. In order to contribute Europe to achieve its goal of a clean and livable environment, new processes with a widely applicable concept are needed for the effective integration of downstream operations in the entire process chain. This will provide cost efficient operations and significantly increase the competitiveness of the European process industry.
MACBETH consortium offers a breakthrough technological advancement by combining the integration of catalytic synthesis and the accompanying separation units into a single, custom-built, extremely effective catalytic membrane reactor (CMR).
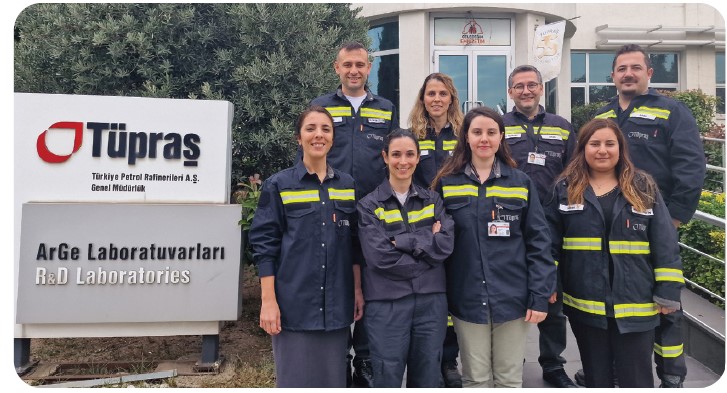
Top Row Left to Right;
Dr. Serdar Çelebi Malzeme ve Reaksiyon Teknolojileri
Alan Lideri / R&D Chapter Lead / Materials and Reaction
Dr. Tuğba Özaltın Ar-Ge Teknik Lideri (SKY)
R&D Technical Lead / Operations & Quality Management
Dr. Cem Açıksarı Ar-Ge Teknik Lideri (Malzeme)
R&D Technical Lead / Materials
Oktay Tunus Ar-Ge Teknik Lideri (Bakım)
R&D Technical Lead / Maintanance
Bottom Row Left to Right;
Feriye Şenol Kaptı Ar-Ge Teknik Lideri (PTY)
R&D Technical Lead / Project & Incentive Management
Merve Caner Ar-Ge Deneyimli Araştırmacı (SKY)
R&D Senior Researcher / Operations & Quality Management
Irmak Su Ökten Ar-Ge Araştırmacı (Malzeme)
R&D Researcher / Materials
Gizem Sultan İş Ar-Ge Araştırmacı (Reaksiyon)
R&D Researcher / Reaction
27 partners with diverse expertise and capabilities in catalytic processes and membrane technologies came together within MACBETH for the first time to be able to transfer technological concept to other sectors of chemical industry.
The MACBETH consortium combines the catalytic synthesis step with the highly efficient separation step via a tailor-made membrane. The preceeding EU funded projects ROMEO, BIONICO and CARENA and further fundamental developments have laid a strong basis by showing the proof of concept for CMRs at TRL 5. Successful pilot plants had been operated for highly relevant and largescale processes:
i) Hydroformylation (HYFO),
ii) Hydrogen production (H2),
iii) Propane dehydrogenation (PDH).
Key members of these consortium have now joined forces in MACBETH to bring and demonstrate CMR to the level of TRL 6/7 and build the basis to move forward for commercialisation of the three novel technologies. Moreover, the knowledge and experiences from these successful European projects provides the basis for tailor-made CMR solutions broadly applicable at significantly different conditions in almost any sector of the process industry requiring separation after catalytic synthesis. In order to demonstrate exploitation level, MACBETH extends the CMR technology to the field of biotechnology which employs bacteria or enzymes as a special forms of catalyst in the biotechnological reactions. In this field, the selective enzymatical cleavage of fatty acids is of particularly
high commercial interest. Demo plant for bio-catalytical oil cleavage (BOC) will be operated and exhibit the commercial applicability of CMR in biotechnology for the first time based on a large variety of already established building blocks (such as catalysts, membranes, support materials and reactor concepts).
The conversion of olefins and syngas to aldehydes, is a key reaction in chemical industry to manufacture specialty chemicals. Hydroformulation (HYFO) case focuses on the optimization of:
i) Support material and structure for efficient use of the catalytic system,
ii) Catalytic system to increase yield and selectivity,
iii) Polymeric membrane for separation efficiency and permeate flow and
iv) Operating parameters. For demo phase, HYFO case will be placed in bypass to
the conventional hydroformylation production plant at Evonik’s Marl site for real industrial-scale conditions.
In H2 case, natural gas or biogas methane is converted to H2 at a much lower temperature by using a novel reactor concept integrating H2 separation in situ during the reforming reaction in a single vessel. This will increase the overall process efficiency (from 59% to more than 70% (for biogas)) and cost effienciency by decreasing volumes & components in the process.
Propylene is a valuable feedstock and it is used to manufacture a number of chemicals and commonly used materials such as polypropylene, acrolein, acetone and polyacrylonitrile. Propylene can be obtained conventionally as a by-product of ethylene production and as a
result of cracking petroleum derived naphtha. Alternative dedicated production process is required to provide adequate propylene supply against to growing demand. Catalytic propane dehydrogenation (PDH) is the most cost-effective alternative to the cracking processes, to bridge the gap between growing global demand and current production capacity. Propane dehydrogenation(PDH) case technology mitigates the required harsh
conditions of selective propane dehydrogenation by optimized low temperature operation (500-550°C) resulting in the avoidance of catalyst deactivation. This will lead to less regeneration steps, improved process management and longer plant/catalyst lifetime. Additionally, the improvement of propylene selectivity significantly reduces gaseous side products in the process stream.
Turkish Petroleum Refineries Corporation (Tüpraş), supplies Türkiye’s energy over 60 years as a leading petroleum company in four refineries (İzmit, İzmir, Kırıkkale, Batman). Tüpraş has committed to mitigate greenhouse gas emissions and become carbon neutral by 2050. In line with this target, Tüpraş shaped its strategy and investment within the scope of sustainable refining, biofuels, zero carbon electricity and green H2 field. Contributing to its strategic goals, Tüpraş takes part in many innovative EU projects, such as MACBETH, aiming to develop processes to reduce greenhouse gas emissions. Tüpraş takes part in PDH
case in MACBETH project and has two main roles.
The first role that was defined during the project proposal phase is to scale up the best performing Pt based PDH catalyst, studied and defined by another project partner University of Salerno (UNISA) in lab scale for use in Tüpraş PDH demo plant. The second role that was decided after the last amendment is to demonstrate PDH at TRL 6 by testing the developed membrane and catalyst in MACBETH project.
Tüpraş has manufactured different catalyst formulations using the Pt based benchmark catalyst defined by UNISA. Promising PDH catalysts shaped via extrusion process and impregnated by Tüpraş, by taking into account the final catalyst compositions defined by UNISA, were tested in Tüpraş PDH plant. After various reaction tests,Tüpraş finally achieved the project target of 95% propylene selectivity and the catalyst remained stable in the long term.
Hence, in the present state, Tüpraş identified the optimum catalyst formulation and reaction conditions to reach the project targets. Tüpraş is going to manufacture up to 1 kg of the best performing catalyst to be used in demo operation. On the other hand, Tüpraş is also working on the revamp of its current plant to TRL-6 level for integrated CMR and its demo operation.
Demo plant is planned to be ready for demonstration and start-up of the PDH pilot plant is planned to be completed within the first quarter of 2024 for 500h continuous operation by using the developed PDH catalyst.
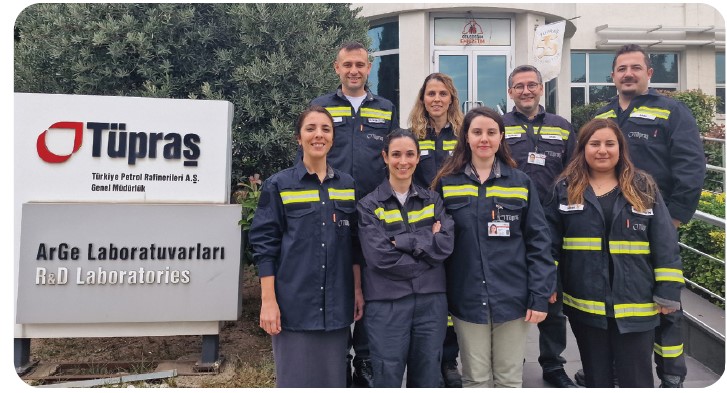
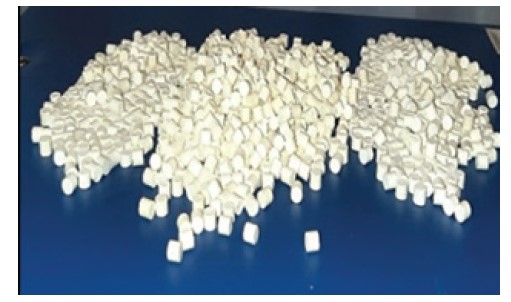