Solventsiz Epoksi Boya ve Kaplamalar
Beton yüzeylerin kaplanması ve korunmasında kullanılan solventsiz epoksi sistemler aşağıdaki gibi özetlenebilir. Bunlar:
1. Solventsiz Epoksi Boyalar:
Aşırı kimyasal dayanım ya da mekanik direnç gerektiği edildiği zaman, solventsiz epoksi boyalar kullanılır. Bunlar tek katta 200-250 mikron kuru film kalınlığı veren koruyucu kaplamalardır.
Çoğunlukla beton tank içi kaplamalarda ve bilgisayar ve benzeri ofis kaplamalarında kullanılır. Dik yüzeyler için, tiksotropik tipleri de bulunur.
2. Solventsiz Epoksi Yer Kaplama:
Solventsiz epoksi boyaların yetersiz kaldığı ve daha yüksek mekanik dayanım gerektiren zeminlerde kullanılır. Malzeme depoları, lastik tekerlekli fork-lift trafiği olan alanlarda kullanıan kaplamalardır. Zeminin trafiğine göre tek kat uygulamayla ve 800-1200 g/m2 harcamayla 400-600 mikron kuru film kalınlığı elde edilir.
3. Solventsiz Epoksi Self Levelling:
Kendiliğinden yayılabilen kaplamalar (self leveling) solventsiz epoksi yer kaplamalarla yüksek dolgulu epoksi harçların (mortar) arasında yer alan kaplamalardır.
Solventsiz epoksi boyaların pratikte istenenlere cevap vermediği ve/ya da daha yüksek mekanik dayanım istendiği yerlerde self leveling uygulanır. Self leveling 1-5 mm arasında kat kalınlığı verecek şekilde emprenye edilmiş beton üzerine uygulanır.
4. Solventsiz Epoksi Mortarlar (Epoksi Harç):
Selflevelling’in mekanik direnç yönünden yetersiz kaldığı durumlarda epoksi mortar sözkonusudur. Burada epoksi rezin/dolgu oranı ortalama 1/ 8 ila 1/9 arasında bir orandadır. Epoksi mortar artık boya ve kaplama ötesinde mekanik dayanımı oldukça yüksek bir epoksi harçtır. Dolayısıyla 10-50 mm kalınlıkta uygulama yapılabilir.
Bunların dışında özel amaçlı Solventsiz Epoksi Multi – Layer Kaplama Sistemleri, solventsiz epoksi Laminasyonlu Kaplama Sistemleri, solventsiz epoksi Anti Statik Kaplama Sistemleri, Su bazlı Epoxy Rezin Kaplama Sistemleri ve solventsiz epoksi Coaltar Kaplama Sistemleri bulunmaktadır.
“Solventsiz boya ve kaplamalar” terimi, yaklaşık 200 mikrondan 50 mm’ye kadar film kalınlıklarında uygulanabilen akışkan kaplama sistemleri olarak tanımlanmaktadır.
Dolayısıyla akışkanlık, solventsiz boyalar, solventsiz yer kaplamalar, self levelling kaplamalar ile yüksek oranda dolgulu epoksi mortarlar arasındaki bağlantıyı oluşturan kriterdir. Solventsiz boya kaplamalar, dolgu maddelerini ıslatmak ve akış özelliklerini oluşturmak için gereken orandan daha yüksek oranda organik bağlayıcı içerir.
Gerekli bağlayıcı içeriği %25 ila %40 arasındadır. Bu oran öteki faktörlerin yanı sıra dolgu maddelerinin en büyük parçacıkların boyutuna da bağlıdır. Bağlayıcı içeriğindeki artış ile akış özellikleri, parlaklık ve yayılma hızı gelişir.
Bununla birlikte, şok ve darbe dayanımıyla birlikte basınç dayanımı aşamalı olarak azalır. Yüksek bir yayılma hızı gerektiğinde arttırılmış bir bağlayıcı içeriğiyle kusursuz bir biçimde ayarlanabilir. Yayılma oranını büyük oranda arttıran uygun mekanik püskürtücülerle uygulamayı kolaylaştırır.
Solventsiz boya ve kaplamalardaki katkı ve yardımcı malzemeler:
Bunlar solventsiz epoksi/ sertleştirici sistemine değişik özellikler kazandırmak için verilen katkılardır.
Seyrelticiler (dilüentler):
Ağırlıklı olarak viskoziteyi düşürmek için solventsiz epoksi sistemlere verilir. Film özellikleri üzerinde de yararlı ya da olumsuz etkileri olabilir. Bunların yanında çam yağı (pine oil) yüzey düzgünleştirmeyi geliştirir.
Benzil alkol, furfuril alkol ve nonil fenol, epoksi rezinler ile sikloalifatik aminler arasındaki reaksiyonu katalize ederler ve aslında bu katkılar olmadan kürleşme tam tamamlanamaz. Bu nedenle, genellikle sertleştirici içine verilirler. Epoksitlenmiş yağ asitleri, malzemenin esnekliği artırır.
Ayrıca dibutilftalat, trifenil fosfit gibi öteki seyrelticiler epoksi rezine verilir. Yüksek derecede uçucu, düşük viskoziteli solventler en yüksek çözme etkisindedirler.
Bununla birlikte, bu tip solventler yüksek film yapılı sistemlerde kullanıldıklarında, ince film kalınlığındaki solvent bazlı boyalar kadar kolay buharlaşamadıklarından sorun yaratabilirler. Kaplamalardaki kalan solventler, güneş ışığına açık yerler gibi özellikle de daha yüksek sıcaklıklarda kabarıp yumuşamaya (blistering) yol açabilirler.
Pigmentler kaplamayı renklendirmek, dolgular ise boya ya da kaplamaya mekanik dayanım kazandırmak için kullanılır. İnorganik bileşikler, çoğunlukla titanyum dioksit (beyaz), krom oksit (yeşil) ve demir oksit (sarı, kırmızımsı kahverengi, siyah) ve bunların karışımları gibi metal oksitler pigment olarak kullanılırlar.
Organik pigmentler, ışık ve kimyasallar etkisinde renk kararlılığı ve aynı zamanda alkalik sertleştiricilerle uyumluluk gerekliliklerini karşılamaları koşuluyla kullanılabilirler.
Barit, talk, kayrak taş tozu, silikatlar, cam yünleri gibi maddeler tipik dolgu maddeleridir. Karbonatlar, yalnızca sistemin asit ortamına açık olmadığı yerlerde kullanılmalıdır.
Dolgu maddeleri, yuvarlak, çubuk şeklinde ya da laminer yapıda olabilirler. Kaplamanın yapısal bileşimi geliştirilebilir ve pigmentasyon maliyeti uygun pigment / dolgu kombinasyonları ile eşzamanlı olarak azaltılabilir.
Birkaçı dışında pigmentler ve dolgu maddeleri hem epoksi rezine hem de sertleştiriciye verilebilir. Bağlayıcı karışımında daha büyük bölüm olduğundan pigment ve dolgular genellikle epoksi rezin komponentine verilir.
Ön karışımların hazırlanmasından önce, dolgu maddelerinin, özellikle de modifiye epoksi reçineler ve sertleştiricilerde çinko kromat gibi bazı pigmentlerden kaynaklanabilen sert çökmeyi ya da viskozite artışını engellemek için uyum ve depolama stabilite testlerinin yapılması önerilir.
Aynı nedenle metalik pigmentlerin sertleştiricilere karıştırılmamalıdır.
Pigmentasyon oranı solventsiz bağlayıcının viskozitesi ile sınırlıdır. Genellikle pigment dolgu konsantrasyonu, toplam karışım üzerinden %30- 50’dir. Pigmentlerin ve dolguların iyi bir dispersiyonunu ve iyi bir ıslanmasını sağlayan üçlü silindirler, dissolver ya da benzeri makineler uygundur.
Kuvars tozu ve silikatlar gibi sert dolgular, silindirlere zarar verdikleri için üçlü silindirle disperse edilmemelidirler. Bunun için dissolver kullanılması önerilir.
Epoksi rezin içinde önceden disperse edilmiş pigment pastaları, pigmentasyon ve bu dolgu maddeleri için uygundur. Karışım oranları hesaplanırken, pastalarda bulunan epoksi rezin dikkate alınmalıdır.
Dolgu maddelerinin nem içeriği:
Atmosferik nemin bir epoksi kaplama ya da boya yüzeyinin oluşumunu etkilediği gibi, dolgudaki nem içeriğinin de kaplamanın ya da mortarın dayanımı üzerinde büyük bir etkisi vardır.
Dolgudaki %1’lik bir su içeriği bile, bir epoksi kuvars mortarın gücünü kuru kuvars ile elde edilen başlangıç değerinden %30 daha düşürür (nem içeriği <%0.1).
Bu nedenle, tipik epoksi dayanım değerleri elde edilmesi gerekiyorsa, solventsiz epoksi rezin içeren formülasyonlar için kurutulmuş dolgu maddesinin kullanılması temel kuraldır.
Dolgulardaki nem içeriği, yalnızca mekanik dayanım üzerinde olumsuz bir etki yaratmakla kalmaz, aynı zamanda özellikle self- levelling kaplama sistemlerinin yüzey kalitesi üzerinde olumsuz bir etki yapabilir. Bu durum, akış özelliklerinin ve parlaklığın yanı sıra filmdeki yüzey etkilerinin azalmasına neden olabilir.
Rezin Tipi Dolgu Katkılar;
bağlayıcı bileşenleri ile reaksiyona girmeyen ürünler olarak tanımlanabilir. Boya ve kaplama maliyetini düşürmek ve bir takım teknik özellikleri iyileştirmek için kullanılırlar. Yeni formülasyonlarda kullanılan tek dolgu olarak hidrokarbon rezinler söylenebilir.
Kömür katranı, toksikolojik yönleri nedeniyle çeşitli ülkelerde yasaklanmıştı. Hidrolik mühendisliği, epoksi katran karışımlarının ana kullanım alanıdır.
Yaklaşık % 40’a kadar olan yüksek katran içeriği büyük ölçüde reaktiviteyi azalttığından azaltılmış reaktivite, hızlı kürlenen sertleştiriciler kullanılarak ya da hızlandırıcılar verilerek düzenlenebilir.
Hidrokarbon rezinler;
dolgu karışımların sınırsız pigment kullanılabilirliğini korumak için gerekli olduğunda kullanılır. Bunun için sıvı ve açık renkli hidrokarbon rezinler uygundur. Yaklaşık olarak %80 -%75 bağlayıcıya %20 – 25 hidrokarbon rezin önerilir.
Daha büyük miktarlar, film özelliklerini etkileyebilir ve bu da migrasyona ve filmin zayıf kürlenmesine neden olabilir. Katkı maddelerinin önerilen miktarlarda verilerek film özelliklerini ve karışıma olan etkisi, kömür katranı verilmesiyle yaklaşık olarak karşılaştırma yapılabilir.
Hidrokarbon rezinler, genel olarak, depolama kararlılığını etkilemeksizin, epoksi rezin bileşenine ve sertleştiriciye önceden karıştırılabilir. Yeni formülasyonlar, ilke olarak depolama istikrarı açısından test edilmelidir.
Yüzey düzenleyiciler;
Orta viskoziteli bağlayıcı karışımlara, özellikle pigment verildiğinde filmde kabarcıklar, çukurlar ya da iğne deliklerine yol açan filmdeki havayı hapsetmek eğilimindedir. Düşük sıcaklıklarda, yüksek atmosferik nemde ve değişken sertleşme koşullarındaki kürleşmelerle farklı dokular oluşabilir.
Bunları gidermek için verilecek katkılara örnek olarak, TEGO Glide 1484, BYK A500 verilebilir. Bu katkılardan bağlayıcı üzerinden %0,3 – %0,6 oranında verilmesi bu etkileri önlemeye yardımcı olacaktır.
Portakal kabuğu görüntüsüne karşı ve yüzey sertliğini arttırmak için Byk 301 %0.1 – 0.2 arasında kullanılır. Byk P104 S, bağlayıcı üzerinde yaklaşık %0.5 miktarlarda, homojen olmayan pigment karışımlarında pigment ayrışmasına karşı etkili olduğu kanıtlanmıştır.
Kuvars içeriğindeki bir artış, kaplama bileşiklerinin viskozitesini önemli ölçüde arttırır. Bu aynı zamanda uygulama sırasında daha yüksek film kalınlıklarına neden olur. Bu nedenle, bir mortar formülasyonundan filmdeki havanın çıkmasına özellikle dikkat edilmelidir.
Silikon yağlarının özellikle etkili katkı maddeleri olduğu kanıtlanmıştır. Sistemdeki havanın daha iyi dışarı çıkabilmesi için dolgunun önceden ıslatılması önerilir ki bu işlem özellikle de kuvars tozunda dolgu yüzeyine yapışan havayı çıkarmak için önerilir.
Bu demektir ki, mortar bileşiğinin teknik özelliklerini ve yüzey kalitesini etkileyebilecek mikro hava kabarcıkları içermediği ya da az sayıdaki mikro kabarcıkları içermesi anlamına gelir.
Tiksotropik Katkılar:
Solventsiz kaplamalar dikey ya da eğik yüzeylere uygulandığında 200-300 μm kalınlığında sarkmayacak filmlerin oluşturması için tiksotropik ajanlar kullanılmalıdır. Silika ya da silikat ve hidrojene hint yağı (Castor Oil) asıllı ürünler bu amaç için uygundur.
Bunlar, uygulandıkları formlar, veriliş yöntemi ve depolama stabilitesi bakımından farklılık gösterirler. Yüksek derecede disperse edilmiş hidrofobik silika (füm silika), uzun süreli tiksotropik etki için özellikle uygundur ve toplam bağlayıcı üzerinden % 2-3 oranında verilir.
Bentone 27 ve 34 gibi Montmorillonit türevleri ksilen ya da ksilen / Antiterra U içinde disperse edildiğinde kullanılabilir.
Thixcin R, Rheocin R, Rilanit Special gibi Hidrojene hint yağı türevleri, etanolde %20’lik pasta ya da nonilfenolde %20’lik solüsyon olarak, bağlayıcı üzerinde %1-2 oranında kullanılabilir.
İyi bir tiksotropik etki için önemli olan katkı maddesinin bağlayıcı içinde ince disperse edilmiş olmasıdır. Montmorillonit eklenmesi, üçlü silindirde ezilerek etkin bir biçimde verilmeyi gerektirir.
Aynı durum, solventin büyük bir kısmını buharlaştırmak için etanol içinde %20‘lik hidrojene hint yağı pastasının verilmesi için de önerilebilir. Silika tipi tiksotropik katkılar bir dissolverde karıştırılarak verilebilir.
Sırlı Yüzeyler için Yapışma Artırıcılar:
Boyaların fayanslara, sırlı yüzeylere ve camlara yapışması, özellikle suya ya da alkalik ortamlara açık bırakıldığında diğer yüzeylere göre daha zayıftır. Yapışmayı arttırmak epoksi rezin için epoksisilanlar, sertleştirici için aminosilanların %3’lük bir oranda her ikisi için bağlayıcı üzerinden verilmesi uygundur.
Uygulama Beton Yüzeylerin Hazırlanması
Bir boya ya da kaplamanın uygulanmasıyla, planlanan işin gerektiği gibi tamamıyla yerine getirebilmesi, yani alt tabakanın hasara karşı korunması için, alt tabakayla koruyucu film tabakasının birbirlerine olduğunca sıkıca yapışması sağlanmalıdır.
Yüzeyin yeterli biçimde hazırlanması kaplamanın iyi yapışması için bir ön koşuldur. Eğer yüzey iyi hazırlanmamış ise, bağlayıcı sistemi ne olursa olsun, baştan kuşkulu sonuçlar ortaya çıkar.
Sulu çimentolu gevşek ve bozuk ya da çimento serpilmiş ince üst beton yüzeylerin dayanımı düşüktür ve penetrasyon için oldukça zayıf kalır. Bununla birlikte, emprenye beton astar verniği bu tip kapalı yüzeylerde yeteri kadar yayılamaz.
Bu nedenle, bu tip uygun olmayan beton tabakaların, tüm beton kaplamalar için önerilen bir emprenye beton astar verniği uygulamasından önce kesinlikle yüzeyden alınması gereklidir.
Benzer durum, aynı zamanda düşük yüzey dayanımı olan “susuz bırakılmış beton” sözcüğü ile tanımlanan kuru ve gevşek beton yüzeyler için de geçerlidir. Yağ, gres, kimyasallar ve benzer maddelerle kirlenmiş yama betonlar çıkarılmalıdır; yüzeyleri solventle temizlemek çoğu zaman yetersiz kalmaktadır.
En güvenli yöntem ise bozuk kısımları kazıyarak çıkarıp atmak ve daha sonra beton yüzeye zarar vermeyen kumlama ile temizlemek ya da alevle yakmaktır.
Yüzey hazırlandıktan ve temizlendikten sonra yüzeyin emprenye beton astar verniği ile doyurulması önerilir. Buradaki amaç, kılcal damarları ve gözenekleri betona kaynaştırarak betondaki tozu bağlamak ve atılacak üst katın daha güvenli bir biçimde betona yapışmasını sağlamaktır.
Beton çok sıkı ve yoğun ise ya da betonun arka bölgelerinde basınç altında zemin suyu beklentisi olduğunda emprenye beton astar verniği kesinlikle gereklidir.
Karıştırma İşlemi:
Uygulama yapılmadan önce, epoksi rezin ve sertleştirici iyice karıştırılmalıdır. Karıştırma işlemi yetersiz olduğunda, rezin ve sertleştirici ayrı kalmaya devam edecek ya da karışım oranı istenildiği gibi olmayacak, dolayısıyla gerektiği gibi beklenen kürleşme gerçekleşmeyecektir.
Sonuç olarak yüzeyde yapışkanlık olacak, zayıf mekanik dayanım ve kimyasal direnç ortaya çıkacaktır. Bu nedenle iki bileşenin doğru karışım oranında karıştırılmasıyla oluşacak üniform ve homojen karışımlar ancak istenen doyurucu film özelliklerini verecektir.
Emprenye beton astar verniklerin iyice karıştırılması optik homojen görünümlerinden anlaşılacaktır. Pigmentli karışımlarda iki bileşenin farklı bir renk pigmentlerden olması karışımın tam gerçekleşmesi açısından yararlı olacaktır.
Uygulama Yöntemleri:
Solventsiz Epoksi boya ve kaplamalar elle ya da makineyle uygulanır. Boya ya da kaplamanın tipi ve viskozitesine bağlı olarak rulo, fırça ya da mala ile uygulanabilir.
En az bir saatlik bir kap ömrü olan orta viskoziteyle düşük viskozite arasındaki epoksi sistemlerin makine ile uygulanması durumunda tek bileşenli püskürtme tabancaları kullanılabilir.
İki komponentli püskürtme tabancaları ise, püskürtme için önceden ısıtılması gereken yüksek viskoziteli sistemler ya da kısa kap ömrü olan sistemler için kullanılır. Solventsiz epoksi boyalar istenilen herhangi bir film kalınlığında uygulanabilir. Dikey yüzeylere uygulama için tiksotropik katkılar verilmelidir.
Solvent bazlı ve emülsiyon boyalarının aksine, bazı durumlarda inceltmek için oldukça uçucu solventler verilmedikçe boya sisteminin birkaç kat atılma zorunluluğu yoktur. Bununla birlikte, daha önce de açıklandığı gibi, beton yüzeydeki ilk katın solvent asıllı emprenye beton astar verniği olması avantajlıdır.
Ayrıca, betondaki tozları bağlamak ve betonun alt yüzeyini ıslatmak için, renksiz, solventsiz bir emprenye astar vernik de kullanılabilir. Çok katlı sistemlerde toplam film kalınlığına bağlı olarak, katlar arası yapışmayla ilgili sertleşme koşulları dikkate alınmalıdır. İki film uygulaması arasındaki olağan zaman aralığı yaklaşık 24 saattir.
Self-levelling mortarların bağlayıcı içeriği yüksek olduğundan, yüksek dolgulu epoksi mortarlardan çok daha kolay uygulanırlar. Büyük ıspatulalar ya da tırtıklı malalar kullanılmalıdır. Kaplama kapasitesi, bağlayıcı içeriğine bağlı olarak, adam başına saatte 15 ila 30 m2 arasındadır. Bu değer, sıva püskürtme makineleri gibi kaplama için uygun bir mekanik püskürtücü kullanıldığında önemli ölçüde yükseltilebilir.
Bu makineler sürekli uygulama olanağı sağlar ve bağlayıcı içeriği daha düşük olan sistemler için de kullanılabilir. Dolgulu kaplamaların püskürtme makinesiyle dikey yüzeylere uygulanmasıyla, maliyetli olan elle malayla uygulamaya gerek duyulmaz. Ancak dolgulu kaplama püskürtülür ve sonra bir malayla düzleştirilir.
Film Kalınlığı:
Uygulanacak minimum film kalınlığı dolgu karışımının maksimum partikül boyutunun yaklaşık 1/3’ü kadardır. Dolayısıyla, kaplamanın koruyucu fonksiyonu, üstten gelen yükten etkilenmez; çünkü partiküller yük ile alt katman arasında doğrudan bir gerilim oluşturmazlar.
Kürleşme Koşulları ve Kür Oranı:
Sıcaklık ve atmosferik nem, iki bileşenli boyaların sertleşmesi ve film yüzey özellikleri üzerinde güçlü bir etki yaratır. Solventsiz epoksi rezin / sertleştirici karışımları, ortam sıcaklığında, düşük sıcaklıklarda ya da yüksek sıcaklıklarda kürlenebilirler.
Hızlı kürlenme yükseltilmiş sıcaklıklarda gerçekleşirken, düşük sıcaklıklarda sertleşme işlemi sertleştiricinin ve epoksi rezinin reaktivitesine bağlı olarak daha yavaştır. Uygulama zorlukları ve kürleşme reaksiyonunun gecikmesi nedeniyle bu sertleştiricilerin 5°C’nin altında kullanımı pratik değildir.
Özellikle tanklar gibi kapalı alanlardaki kürleşme koşullarını iyileştirmek için, yalnızca ortamdaki havayı değil aynı zamanda yüzeyi de ısıtabilen kızıl ötesi radyatörler ya da sıcak hava üfleyiciler kullanılabilir.
Bu durum, boyanın uygulama sırasındaki ıslanma zorluklarını ve uygulanan yüzey tarafından soğutulması zorluklarını ortadan kaldırır.
Söz konusu standart sertleştiriciler, standart bir iklimde (23°C / %50 bağıl nem ve 23°C ve %95 bağıl nem) sertleştiğinde, bir haftadan kısa bir kürlenme süresi içinde yapışkan olmayan yüzeyler sağlar.
Düşük sıcaklıklarda, sertleştiricilerin reaktivitesine bağlı olarak ve özellikle bazı özel sertleştiriciler kullanıldığında, biraz gecikme olsa da yapışmaz bir kürleşme gerçekleşir. Ancak bazı sistemlerde az miktarda kalıntı bir yapışkanlık kalabilir.
Kap Ömrü:
Kap ömrü, sertleştiriciyle epoksi rezin karıştırılmasından hemen sonra başlar ve jelleşme oluşumunun kısa bir süre öncesinda sona erer. Kap ömrü aşağıdaki etkenlerle değişir:
• Modifiye epoksi rezinlerinin kap ömrü biraz daha uzundur.
• Sertleştiricinin tipiyle değişiklik gösterir.
• Kap ömrünü uzatan dolgu maddeleri verilmesiyle değişir.
• Karışımın başlangıç sıcaklığıyla değişir. Yüksek karışım sıcaklıklarıyla kap ömrü azalır.
• Karışımın büyüklüğüyle değişir. Epoksi rezinlerle sertleştiriciler arasındaki reaksiyondan ısı açığa çıkar. Karışım ne kadar büyük olursa ısı çıkışı (egzoterm) o kadar büyük olur.
Bu nedenle, karışımların büyüklüğü, çalışma için gerekli zamana uyacak biçimde olmalıdır. Bunun için karışımı daha küçük boyutlarda hazırlamak daha uygun olacaktır. Ayrıca oluşan ısının başka bir biçimde dağılmasını sağlamak, ısınmasını engelleyici soğutma sistemi gibi öneriler olabilir.
Viskozitede ya da karışım sıcaklığındaki bir artış, bağlayıcının reaktivitesine ve karışımın boyutuna göre değişir. Kap ömrünün sonunda uygulama yapmak artık mümkün değildir ve film oluşumu yetersizdir. Düşük viskoziteli sikloalifatik poliamin sertleştiriciler 40°C’de 15 dakika sonra jel olur.
“Self-levelling Mortarlar” ile çalışırken, kullanılan bağlayıcının reaktivitesi daha az önemlidir, çünkü mortar nispeten basit ve hızlı bir şekilde uygulanabilir.
Çok kompakt kütlelerde ekzotermik ısıtma ile çok hızlı bir şekilde kürleşebilen, yüksek reaktiviteli sertleştiricili kaplama sistemleri, ısı birikimini önlemek için karıştırıldıktan hemen sonra kaplanacak yüzeye yayılmalıdır. Kürleşme, yayılma problemlerini önlemek için belirli bir yüzey sıcaklığında oluşturulmalıdır.
Su Etkisinde Renk Değişikliği:
Belirli koşullar altında, suyun sertleşmiş boya ve kaplamalara etkisi sonucu, boya ve kaplama yüzeyinde renk solması oluşabilir. Bu, sertleşme koşullarına ve kullanılan sertleştiricinin türüne bağlıdır. Bu etki, alifatik poliamin bazlı sertleştiricilerde daha belirgindir.
Sikloalifatik poliaminler solmaya karşı daha az duyarlıdır, ancak poliaminoamidler pratik olarak etkilenmezler. Sertleşme koşullarının yaşamsal önemi vardır.
20°C civarında ve %95’e kadar bağıl nemlerde pratik olarak renk değişikliği gözlenmezken, bu etki daha düşük sıcaklıklarda artan nemle birlikte daha şiddetli olur. Bu etki, sıcaklığın çiğlenme noktasının altına düştüğü durumlarda sertleşme sırasında hızlı soğuma ile sonuçlandığından özellikle kritiktir.
Üst tabakanın hidrasyonu nedeniyle sertleşmeden önce kaplama üzerinde ince bir su filmi oluşur. Bu durum parlaklığı azaltır ve uzun süreli sertleşme sonrasında bile su etkisinde kaldığında güçlü bir duyarlılığa neden olur. Bu etki hem renksiz hem pigmentli kaplamalarda da vardır.
Görsel izlenim, parlak renkli pigmentlerle daha belirgin olmasına karşın soluk renklerle daha az gözlenir. Kritik koşullar altında sertleşme gerçekleştikten sonra suya karşı duyarlılığı azaltmak için önerilen önlemler olarak, sertleştirici içinde bazı poliaminoamidlerin kullanılması ve aynı zamanda silikon yağı verilmesidir.
En etkili silikon kullanım oranı bağlayıcı üzerinden % 0.2-0.6 oranında TEGO Glide B1484 olduğu kanıtlanmıştır. Kapalı tankların kızılötesi radyatörlerle ya da sıcak hava üfleyicileriyle ısıtılması tüm sertleşme süresince avantajlıdır.
Benimsenen önlemler ne olursa olsun, tatmin edici kürlenmeyi sağlamak için kaplamayı uygulamadan önce sertleşme koşullarıyla uyumlu duruma getirmek gereklidir.
Arakatlarda Yapışma:
Sıcaklık düştüğünde henüz sertleşmemiş film üzerinde yoğunlaşan yüksek atmosferik nem, daha düşük yapışmayı yol açan hidrasyon sonucunda film yüzeyini değiştirir. Kaplama, olumsuz sertleşme koşullarının etkisinde ne kadar uzun süre kalırsa etki o kadar fazla olur.
Burada da, uygun önlemleri planlamak için verilen sertleşme koşullarındaki ön testler önerilir. Standart bir sıcaklıkta sertleşme gerçekleştiğinde, standart Epoksi rezin / sertleştirici sistemlerin katlar arasında iyi bir adezyonu vardır. Ardışık kat uygulamalarında daha uzun aralıklardan kaçınılmalıdır.
Özellikle kaplamalar daha sonra su etkisinde kalacaksa, birkaç gün bile uygulama yapmadan kat aralarının açık kalması dezavantajdır. Bu tip durumlarda ve olumsuz koşullar altında olan sertleşmelerden sonra yüzeyin hafifçe pürüzlendirilmesiyle yeniden iyi yapışma sağlanabilir.
Formülasyon Önerileri Suyun Atmosferik Nemliliğinin Etkisi:
Bağlayıcı yüzeyinin kısa bir sertleşme süresinden sonra değişken su duyarlılığı vardır. Bu durum daha açık bir renk ya da beyaz bir renk olarak sonuçlanabilir. Bu bazen pratik uygulama zorluklarına neden olabilir.
Formülasyonun optimum su performansını incelemek için basit, çok etkili bir laboratuar testi bulunmaktadır. Kürleşme sonrasında ve farklı koşullar altında kaplamaya su damlacıkları uygulayarak yapılır. Damlacıklar kısa bir süre sonra kesilir ve yüzeyin renk kaybı derecelendirilir.
Termal Genleşme:
Termal genleşme katsayısının etkileşimi, film kalınlığı, esneklik modülü ve maksimum sıcaklık farkının uygulanan koruyucu kaplamanın başarısını belirler. Bu, açık havadaki kaplamalar için özellikle önemlidir.
Self-levelling mortarın ısıl genleşme katsayısı ne kadar büyük olursa, kaplama kalınlığı o kadar incedir. Bu, beton yüzey ile mortar arasındaki yapışma bölgesinde büyük gerilimi önlemek içindir.
Olumsuz koşullar altında gerilim kuvvetleri, yüzeyin gerilme kuvvetini aşabilir, böylece epoksi sistemlerinin iyi yapışma gücü nedeniyle alt tabakada bir kırılma olacaktır.
Uzun Süreli Performans:
Epoksi rezinlerin oda sıcaklığında reaksiyonları, reaktiviteye bağlı olarak, temel olarak 1-7 gün içinde tamamlanır. Uygulama sonrası birkaç hafta boyunca, kürleşme sonrasında güçte bir artış daha ortaya çıkabilir. Altı ay boyunca basınç dayanımı ve özellikle bükülme dayanımı 7 günde gücü %110-120’ye yükseliyor.
Kürleşme sonrası bu güç artışına paralel olarak, özellikle kritik ortamlarda belirgin bir gelişme sağlayabilecek kimyasal direnç de artmaktadır. Açık havadaki mortar testlerinin sonuçları, kontrollü iklim koşullarında yapılan 6-10 yıl sonrasında bile aynı kalmıştır.
Dış Ortama Dayanıklılık:
Epoksi rezinli boya ve kaplamalar, dış ortam koşullarında kaldıklarında olumsuz değişikliklere uğrarlar. Bunlardan tebeşirlenme ve parlaklık kaybı belirgin sonuçlarıdır.
UV radyasyonla ve nem arasındaki etkileşim, bağlayıcının üst tabakasını alıp çıkarır ve pigment parçacıklarını açığa çıkararak parlaklık kaybına yol açar ve daha sonra da pigmentin çıkmasına neden olur.
Bununla birlikte, toplam film kalınlığına bağlı olarak yüzeydeki hasar çok hafiftir, bu nedenle koruyuculuk işlevinde bir zayıflama beklenmemektedir. Tebeşirlenme, havaya bağlı olarak ilk 3 ya da 6 ay sonra görülebilir.
Tebeşirlenme ve parlaklık kaybının nedeni epoksi rezinlerin aromatik bazıdır. Sertleştiriciler ikinci derece önemdedir.
Aynı zamanda sararma da oluşabilir, ancak bu sararma yalnızca ışık etkisiyle oluşur. Sararmanın derecesi, büyük ölçüde sertleştiriciler tarafından belirlenir. Bu etki, sikloalifatik tip sertleştirici ile hafifçe sararmış görülürken aromatik tip sertleştirici ile karşılaştırıldığında daha belirgin bir sarılık gözlenmiştir.
Dış ortam dayanım testinin, doğal hava koşullarında test edilmesi zaman alıcıdır ve “yapay hava koşulları” olası bir alternatiftir. Test sonuçlarını karşılaştırırken, zaman boyutu da dikkate alınmalıdır.
Yol Gösterici Örnek Formüller:
Aşağıdaki formülasyonlar pigmentsiz ve pigmentli karışımları kapsar. Bunlar spesifik amaçlar için hazırlanan formülasyonlar olup, daha sonraki yapılması gereken geliştirmeler için bir temel oluşturan bazı sertleştiricilerle epoksi bağlayıcı formülasyonlarına örnektir.
Beton Astar Verniği:
Düşük viskoziteli bir beton astar verniği, beton ve benzeri yüzeyler gibi emici alt tabakalara iyi yayılma gücündedir.
Beton kaplamalar için emprenye beton astar verniği, gözenek doldurma, uygulanacak boya ve kaplamalar için yeterince güçlü bir zemin oluşturmak üzere üst beton tabakanın güçlendirilmesi, yapışma zayıflığını oluşturan tozların betona bağlanması gibi işlevlere sahiptir.
Bu amaçla, yüksek nemli ortamlarda, hemen hemen yağlı bir film ya da yüzey yapışması olmadan yüzeyde sertleşen, bağlayıcı formülasyonları kullanılmalıdır.
Atmosferik nem yüksek olduğunda ya da uygulama ve sertleşme sırasında zeminde ıslaklık olduğunda, neme ve ıslaklığa duyarlı sertleştiriciler kullanıldığında, boya ya da kaplamada zayıf bir yapışma oluşabilir. Bu olumsuz etki hidrasyondan kaynaklanır ve daha büyük ve daha higroskopik sertleştirici oluşur.
Dolayısıyla beton astar verniğini de daha fazla nem etkilemiş olur. Buradaki sorunda, bağlayıcı sistemin reaksiyon hızı ve beton kalitesi ve gözeneklilik gibi bir takım öteki faktörler de rol oynamaktadır.
Düşük viskoziteli solventsiz beton astar verniklerinin popülaritesi, özellikle betonda kalan solventin buharlaşmasını beklemek zorunda kalmadan zamandan kazanmak faktöründen kaynaklanmaktadır.
Bu sistemlerde solvent verilmesi %5’ten fazla olmamalıdır. Bununla birlikte, solventsiz beton astar verniklerinin solvent bazlı ürünlerden daha düşük betona yayılma yeteneğinde olduğu dikkate alınmalıdır
Tablo 1: Örnek bir Solventsiz Emprenye
Beton Astar Vernik Formülü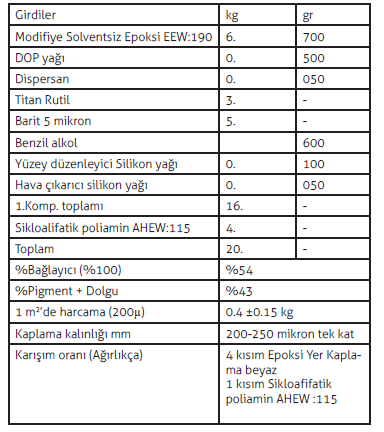
Tablo 2: Örnek bir Solventsiz Epoksi Yer Kaplama-Beyaz formülü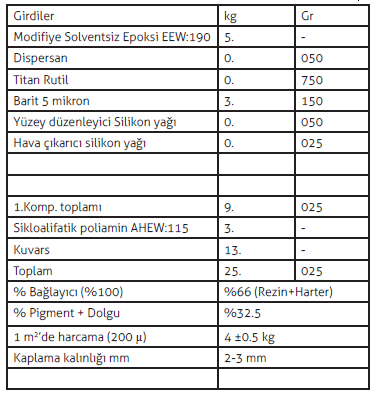
Tablo 3: Örnek bir Solventsiz Epoksi Self-Leveling-Beyaz formülü
M. Namık Kayaalp – Kimya Mühendisi / Ecelak Boya Kimya Ltd. Şti.
Kaynakça
1. Newton, D.S. (Ed.), Paint Technology Manual Part 4, Chapman and Hall, London
2. Paint Formulation, J.Boxal, Geoge Godwin Ltd.-London 1980.
3. SCHERING Industrie-Chemicalien, Bergkamen1 Germany, 1978
4. UPPC GmbH, Schemmerberger strasse 39, Baltringen, Germany, 1997
5. Huntsman Advanced Materials (Switzerland) GmbH Klybeckstrasse 200 P.O. Box 4002 Basel Switzerland
6. Epoxy Polymers, Edited by Jean-Pierre Pascault and Roberto J. J. Williams, WILEY-VLH Verlag umbH.
7. Paint and Coating Testing Manual Fifteenth Edition of the Gardner-Sward Handbook, Joseph V. Koleske,