Yeni Nesil Afromer Serisi Köpük Kesiciler ve Kaplama Endüstrisindeki Etkin Performans Analizi
1. Giriş
Köpük, homojen olmayan tüm sıvı boya sistemlerinde, makro ve/veya mikro boyutta oluşan hava kabarcıklarıdır. Üretim sürecinde ya da uygulama esnasında meydana gelebilmektedir. Üretim sürecindeki oluşumuyla eksik miktarda ambalajlamaya, uygulama esnasındaki oluşumuyla da yüzey kusurlarına neden olmaktadır.
Yüzey aktif madde içermeyen saf bir sıvıda oluşan makro köpükler, sıvının yüzeyine ulaştığında kendiliğinden patlayıp söner. Yüzey aktif madde (ör: ıslatıcı, dispersiyon ajanı vb.) içeren boyalarda ise sıvının iç ve dış yüzeyinde makro ve mikro köpükler oluşmaktadır.
Köpük kesici olarak nitelendirdiğimiz katkı maddeleriyle oluşan köpüğü ortadan kaldırmak veya oluşumunu engellemek mümkündür.
Türkiye, sektörel yapısı itibarı ile Avrupa’nın 5. boya üreticisi konumundadır. Toplam üretim kapasitesinin %55’ini su bazlı boyalar %45’ini solvent bazlı boyalar oluşturmakta olup, sektörde %35 yerli hammadde kullanılmaktadır (1).
Sektörün toplam boya üretim kapasitesi ise yaklaşık 800 bin ton/yıl olup, kapasite kullanım oranı %65 düzeyindedir. Bu verilere dayanarak sektördeki köpük kesici ihtiyacı/kullanımının yaklaşık 20-30 bin ton/yıl aralığında olduğu öngörülmektedir.
2. Köpük Oluşumu ve Kesme Mekanizması Sıvı, yüzey aktif madde (ör: dispersiyon ajanı, ıslatıcı vb.) içeriyorsa iç ve dış yüzeyinde köpük kabarcıkları oluşur (2). Bunun yanında; formülasyonun içerdiği selüloz türevleri ve reçinelerin varlığı da köpük oluşumuna
sebep olmaktadır.
Saf sıvılar köpürmez. Köpüğün yüzeye çıkma hızının köpük yarıçapı ve sıvının viskozitesine göre korelasyonu Stokes yasası ile açıklanmaktadır. Stokes yasası Şekil 1’de belirtilmiştir.
Stokes Yasası’na göre oluşan köpüğün yüzeye yükselme hızı (V); kabarcıkların yarıçapına (r) ve sıvının viskozitesine (η) bağlıdır. Sıvı fazın viskozitesi ne kadar büyük olursa, kabarcıklar o kadar yavaş yükselir.
Viskozitesi çok yüksek bir sıvıda oluşan mikro köpükler genellikle sıvının yüzeyine ulaşamaz. Makro boyutta oluşan köpükler ise sıvının yüzeyine ulaşarak yüzey aktif madde içeren bir tabaka ile kaplanır.
Köpük kabarcıklarına tutunan köpük kesici damlacıkları, bu köpük tabakasına nüfuz ederek yüzey aktif maddelerin yerini alır. Köpük kabarcıklarını bu tabakanın yüzeyinden uzaklaştırarak patlamasını sağlar. Köpük kesme mekanizmaları Şekil 2’de gösterilmiştir.
Boya yüzeye uygulandığında, çözücünün aniden buharlaşması sonucu reçine çözeltisinin viskozitesi belirgin ve hızlı bir şekilde artar. Böylece küçük mikro köpükler genellikle boyadan tamamen kurtulur ve kaplamanın yüzeyinde iğne deliklerine neden olur (3).
Köpük kesiciler; köpük giderilecek ortamda çözünmeyen ve düşük yüzey gerilimine sahip yapıda olmalıdır. Farklı formülasyonlara sahip olan su, solvent veya solventsiz boyalar için uygun köpük kesiciyi seçmek gerekir.
İyi bir köpük kesicinin sahip olması gereken özellikler:
• Çözelti içerisinde iyi dağılmalıdır.
• Çözelti ile reaksiyona girmemelidir.
• Yüksek yayılma katsayısına sahip olmalıdır.
• Yüzey gerilimi çözeltininkinden düşük olmalıdır.
• Artık madde bırakmamalıdır.
Belirli bir formülasyon için uygun köpük kesiciyi seçerken öncelikle ürünün bazına (su, solvent, epoksi, akrilik vb.) uygun olup olmadığına bakılmalıdır. Köpük oluşum eğilimi benzer kaplama sistemleri için dahi farklılık gösterebilmektedir.
Aktif madde miktarı bu konuda önemli parametrelerden biri olarak değerlendirilebilir. Aktif madde oranı %100’den düşük olan köpük kesiciler emülsiye edilmiştir. Suyla emülsiye edilmiş bir köpük kesicinin içerdiği su miktarına göre boya formülasyonundaki su miktarı ayarlanmalıdır.
Dolayısıyla formülasyon için seçtiğimiz köpük kesicinin aktif madde miktarı göz önünde bulundurulmalıdır. Kullanıldığı sisteme uygun olmayan bir köpük kesici boyayla homojen olarak karışmaz, yüzeyde gözle görülecek şekilde kusmalara neden olur.
Aynı zamanda balık gözü, iğne deliği, yüzeyde yağlanma, harelenme, boyada açma gibi sorunlarla da karşı karşıya kalınabilir.
4. Köpük Kesici Türleri
Köpük kesicileri çok farklı şekillerde kategorize etmek mümkün olmakla birlikte sıvı ve toz köpük kesiciler olarak iki genel bölümde değerlendirebiliriz. Bunun yanı sıra silikon bazlı, yağ bazlı, mineral bazlı, solvent bazlı olarak da sınıflandırılabilmektedir.
Bu makalede mineral yağ, silikon ve polimer esaslı köpük kesicilere yer verilmiştir. Tablo 1‘de Reaksiyon Afromer® serisi köpük kesici grupları bazlarına göre kategorize edilmiştir.
3.1. Sıvı Köpük Kesiciler
Tüm su bazlı boya sistemleri için kullanımı uygundur. Formülasyonda %0,3-0,5 aralığında kullanılır. Kullanıldıkları su bazlı sistemlerde; makro ve mikro boyutta oluşan köpüğü keser ve tekrar oluşumunu önlerler.
3.1.1 Mineral Yağ Esaslı Köpük Kesiciler
Mineral yağ esaslı köpük kesiciler, sudan daha düşük bir yüzey gerilimine sahiptir. Film tabakasında; balık gözü, krater gibi film yüzeyini bozacak bir yapıya neden olmazlar. Diğer köpük kesicilerin aktif olamadığı yoğun v dirençli sistemler için kullanımı uygundur.
Su bazlı endüstriyel boyalar, baskı mürekkepleri, su bazlı pigment pasta, tekstil gibi üretim alanlarında kullanılabilmektedir. Fenolik yapı, silikon ve uçucu bileşen içermezler. Maliyet olarak tüketiciye avantaj sağlamaktadırlar. Reaksiyon Afromer® serisi mineral yağ esaslı köpük kesiciler Tablo 2’de listelenmiştir.
Aynı formülasyona sahip su bazlı bir boyada farklı köpük kesiciler kullanılmış ve kaplama sonrası görünümleri köpük kesici kullanılmayan kaplama ile karşılaştırılmıştır.
Karşılaştırmalar Şekil 4’te sırasıyla (a) köpük kesici kullanılmayan, (b) rakip ürün, (c) Afromer® serisi köpük kesicinin oluşturduğu yüzeyin daha pürüzsüz olduğu ve köpükleri büyük oranda ortadan kaldırdığı görülmektedir.
Şekil 5’te soldan sağa doğru sırasıyla Afromer® SE20, Afromer® S10 ve Afromer® S30 ürünlerinin fiziksel görünümleri yer almaktadır.
3.2 Toz Köpük Kesiciler
Toz köpük kesiciler prensip olarak silika gibi partikül bir taşıyıcı üzerinde yağ bazlı köpük gidericilerdir. Bunlar toz boya, çimento, alçı ve deterjanlar gibi bütün toz ürünlere eklenir.
Yapı grubunda formülasyondaki kuru bileşenin toplam miktarına göre %0,05- 0,5 aralığında kullanılır. Çimento, alçı gibi ürünlerde kullanımıyla sızdırmazlığın artmasına yardımcı olur.
Deterjandaki kullanımıyla aşırı köpürmenin ortadan kalkmasını sağlar ve istenen optimum köpüğü dengede tutar. Deterjanda ise %0,05-0,3 aralığında kullanılması tavsiye edilmektedir.
3.2.1 Polieter Esaslı Toz Köpük Kesiciler
Modifiye edilmiş özel polimerlerin karışımından oluşur. Kullanıldığı ortamdaki hızlı dağılma özelliği sayesinde oluşan köpüklerin hızla yok olmasını sağlarlar. Maliyet olarak hidrokarbon esaslı toz köpük kesicilere göre daha pahalıdır.
Fazla kullanımına bağlı olarak yüzey kusuru oluşturmazlar. Uçucu bileşen içermezler.
Reaksiyon Afromer® serisi polieter esaslı toz köpük kesici teknik detayları Şekil 6’da verilmiştir.
3.2.2 Hidrokarbon Esaslı Toz Köpük Kesiciler
Mineral yağ esaslı sıvı köpük kesicilerin toz halidir. Maliyet olarak uygundur. Optimum kullanım miktarının üzerinde kullanımı yüzey kusurlarına (yağlanma gibi) neden olabilir. Hidrokarbon esaslı Afromer® P2202 ürününün özellikleri Şekil 7’de belirtilmiştir.
Afromer® P 1850 ve Afromer® P 2202 ürünlerinin fiziksel görünümleri ise Şekil 8’de yer almaktadır.
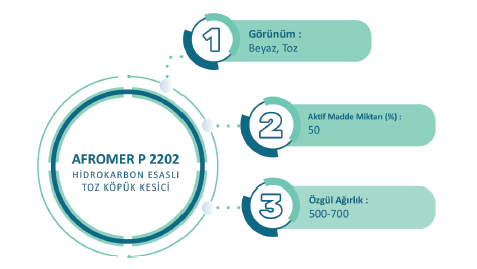
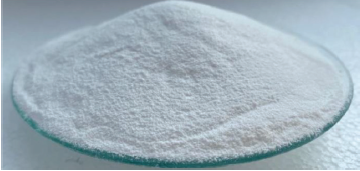
Şekil 9’da ise sırasıya (a) köpük kesici kullanılmayan çimento harcı yüzeyinde oluşan köpük kabarcıkları (b) aynı formülasyon ile hazırlanan çimento harcında Reaksiyon Afromer® serisi toz köpük kesici kullanılmıştır ve yüzeydeki köpükler giderilerek pürüzsüz bir görünüm elde edilmiştir.
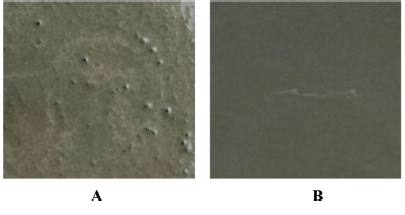
Şekil 10 (A)’da köpük kesici kullanılmayan alçı yüzeyinde oluşan köpük kabarcıklarının oluşturduğu krater sorunları gözlemlenmektedir. Oluşan kraterler yüzey bütünlüğünü bozar ve mukavemetin azalmasına neden olur.
Şekil 10(B)’de ise aynı formülasyon ile hazırlanan alçıda Afromer® serisi toz köpük kesici kullanılmıştır ve yüzeydeki köpükler giderilerek pürüzsüz bir görünüm elde edilmiştir. Herhangi bir yüzey kusuru gözlemlenmemiştir.
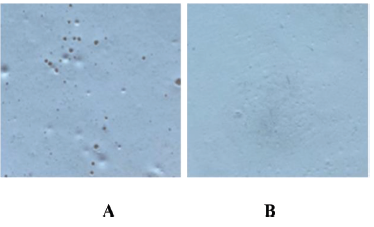
Tablo 4. Afromer® serisi köpük kesici ürünlerin başlıca kullanım alanları
4. Test Yöntemleri
4.1 Sıvı Köpük Kesicilerin Testleri
4.1.1 Mezür ile Hacim Ölçümü
Belirli bir formülasyon için hazırlanan boya numunesinden 50 gr kadar tartılır. Bir karıştırıcı yardımıyla 1500 rpm hızla 1 dakika kadar karıştırılır. Sonrasında 3000 rpm hızla 1 dakika kadar daha karıştırılır.
Mezür yardımıyla hacmi ölçülür ve not edilir. Daha sonra köpük kesici 0,2 oranında ilave edilir. Aynı işlemler tekrarlanır. Mezürdeki yeni hacim ölçülür ve not edilir. Diğer köpük kesicilerle yapılan performans kıyaslaması mezürde ölçülen hacim artışına göre değerlendirilir.
24 saat sonra boyalar karıştırılır, fırçayla ya da rulo ile uygulanır ve film bütünlüğü, renk kabulü, parlaklık, yapışma ve pürüzlülük açısından kuru filmde değerlendirilir. Hacim artışı daha az olan köpük kesicinin performansının daha iyi olduğu sonucu ortaya çıkar.
Mezürde yapılan bu hacim testinde makro köpükler ölçülür, mikro köpükler ise kısmi oranda ölçülebilir. Afromer® M20 ve muadil ürünlerin karşılaştırmalı köpük kesme performansı Tablo 5‘te listelenmiştir.
Tablo 5. Mürekkep içerisinde 1 aylık periyotta Afromer® M20 ve muadil köpük kesici testi sonuç kıyaslaması
Tablo 5’te Afromer® M20 ve muadil köpük kesicilerle hazırlanmış olan numunelerin belirli periyotlarda mezür ile hacimleri listelenmiş ve köpük kesicinin sonradan oluşabilecek köpüğü ortadan kaldırma performansı değerlendirilmiştir.
30 günlük süre sonunda hacmi en az artan Afromer® M20 ürününün köpüğün uzun
vadede oluşumunu büyük oranda engellediği görülmektedir.
4.1.2 Piknometre ile Yoğunluk Ölçümü
Mikro köpüklerin tespiti için metal piknometre ile yoğunluk ölçümü yapılmaktadır.
Bu metot ile köpük kesici eklenmiş numunelerde hacim azalması izlenerek köpüğün stabilizasyonu gözlenmektedir. Piknometre önce boş olarak, ardından numuneyle doldurulmuş olarak tartılır.
Kütle farkının piknometrenin hacmine bölünmesi numunenin yoğunluğunu verir. Aynı formülasyona ve kütleye sahip boyalarda farklı köpük kesicilerin test edildiği numunelerde; yoğunluk artışı olması durumunda hacmin azaldığı dolayısıyla köpüğün giderildiği öngörülmektedir.
Bu metot ile köpük kesici eklenmiş numunelerde hacim azalması izlenerek köpüğün stabilizasyonu gözlenmektedir. Piknometre önce boş olarak, ardından numuneyle doldurulmuş olarak tartılır.
Kütle farkının piknometrenin hacmine bölünmesi numunenin yoğunluğunu verir. Aynı formülasyona ve kütleye sahip boyalarda farklı köpük kesicilerin test edildiği numunelerde; yoğunluk artışı olması durumunda hacmin azaldığı dolayısıyla köpüğün giderildiği öngörülmektedir.
Tablo 6’da bir boya formülasyonunda kullanılan Afromer ® M10, Afromer® M15 ve rakip köpük kesicilerin kullanım miktarlarına bağlı olarak değişen yoğunlukları piknometre ile ölçülmüştür.
Yoğunluğu en yüksek olan Afromer® M10 ve Afromer® M15 in düşük kullanım miktarlarında, oluşan köpükleri en yüksek oranda söndürdüğü gözlenmiştir. Afromer® M10 ve Afromer® M15 ürünleri aynı kullanım miktarı ile en yüksek köpük kesme performansı göstermiştir.
4.2 Toz Köpük Kesicilerin Testleri
Hazırlanan çimento veya alçı bazlı karışım belli bir kalıba dökülür ve yayılır (Şekil 10(A)). Aynı formülasyona ait karışıma %0,3 gr toz köpük kesici eklendikten sonra karışım ayrı bir kalıba dökülür (Şekil 10(B)).
Her iki kalıptaki çimento harcı/alçı yüzeyi incelenir. Bu yüzey testi ile büyük oranda makro köpükler gözlemlenir ve yorumlanır. Mikro köpüklerin gözlemlenmesi için piknometre ile yoğunluk testi yapılır.
Köpük kesiciler düşük kullanım oranlarına rağmen son ürün kalitesine büyük oranda etki etmektedir. Dolayısıyla en uygun köpük kesicinin seçimi ve en doğru şekliyle değerlendirilmesi önem kazanmaktadır.
Köpük kesici seçimleri boya formülasyonuna uygun olarak seçilmeli ve etkinliği çözeltide kullanılan farklı katkılar ile etkileşimi göz önünde bulundurularak test edilmelidir. Reaksiyon Kimya Uzman Ar-Ge ekiplerinin uzun yıllara dayalı tecrübeleri ile geliştirilen Afromer® serisi köpük kesicilerin kullanımı ile; makro ve mikro köpükleri kısa ve uzun vadede ortadan kaldırmak, kusursuz bir yüzey elde etmek mümkündür.
Mikro köpükleri ortadan kaldırma performansı göstermesi nedeniyle hava atıcı olarak da kullanılabilirler. Uçucu bileşen, APEO ve NPE içermezler. Kullanıldığı ürünün renginde herhangi bir değişikliğe neden olmazlar. Fiyat performans olarak tüketiciye büyük oranda avantaj sağlamaktadır.
Reaksiyon Kimya
Reaksiyon Kimya A.Ş. 20 yıla yakın süredir inşaat malzemeleri pazarının ihtiyaç duyduğu hammadde tedariği ve üretim faaliyetlerini gerçekleştirmektedir. Epoksi sertleştiriciler, su bazlı pigment pastalar, akrilik emülsiyonlar, toz su iticiler, toz ve sıvı hiper akışkanlaştırıcılar,
waxlar, solvent bazlı akrilik reçineler ve köpük kesiciler üretimini gerçekleştirdiği ana ürün
gruplarından bazılarıdır.
Reaksiyon Kimya Anonim Şirketi, Kocaeli Dilovası Organize Sanayi Bölgesi’nde 4500 m² alana kurulmuş olan modern teknoloji ile donatılmış fabrikasında üretim yapmaktadır.
Firmanın bütün iş operasyon süreçleri müşteri memnuniyetinin sağlanabilmesi amacıyla tam donanımlı bir Ar-Ge ve kalite kontrol departmanı tarafında desteklenmektedir. Ar-Ge çalışmalarına verdiği önem ile üretim hacmini büyüterek Türkiye’nin bu sektörde dışa bağımlılığını azaltmak yegâne hedefi olmuştur.
Kaynaklar
1) Boya Sektörü Mart’21 (www.ticaret.gov.tr)
2) http://en.wikipedia.org/wiki/Foam
3) Bodo Müller, Understanding Additives, Vincentz Network, 2010