Dolguların Tanımı
Dolgu pigmentler ya da daha kısa adıyla dolgular, genellikle bir boya formülasyonunun maliyetini düşürmek için kullanılır. Bununla birlikte,boyanın akış,viskozite,çökme kararlılığı, film sağlamlığı gibi özelliklerini de değiştirebilirler.
Dolgular,bağlayıcıda ve çözücülerde çözünmeyen ve film üzerinde opaklaştırıcı ya da renklendirici etkisi olmayan ya da çok az örtücülük etkisi olan boya katkı maddeleridir. Sıvı boyanın akış özelliklerini ve ayrıca boya filminin mekanik geçirgenliğini,parlaklığını ve yayılma özelliklerini değiştirmek için kullanılırlar.
Dolgular temel olarak, adından da anlaşılacağı gibi, bir boyanın pigmentasyonunu ekonomik bir malzeme ile doldurmak için kullanılır. Bununla birlikte, bunu yaparken, dolguların boyaya verebileceği bir takım özellikler vardır ve bunlar, dolguların değerine ve kullanımına katkıda bulunurlar.
Örneğin, boyanın viskozitesini kontrol etmek, akış özelliklerini iyileştirmek ve daha ağır pigmentlerin sert bir şekilde çökmesini en aza indirmek için kullanılabilirler. Dayanıklılık ya da matlaştırma kolaylığı özellikleri verebilirler ve maksimum ara kat yapışmasını sağlayan yüksek kaliteli astar üretimine olanak sağlayabilirler.
Bir dolgu maddesinin pigmentleme özelliklerini ne ölçüde uygulayabildiği, temel olarak kırılma indisiyle ilgilidir. Polimerlerin çoğunun kırılma indisi yaklaşık 1.5’tir ve bu nedenle, 1.7’den daha düşük değerlerde olan minerallerin çoğu, boya ve polimerin opaklığına hiçbir biçimde katkıda bulunmaz ve gözle görülür bir örtme gücü de yoktur.
Ancak kırılma indisi yaklaşık 2,7 olan TiO2 ile karşılaştırıldığında çok az opaklaştırma etkisi verirebilir. Bir dolgunun kırılma indisi 1.7’yi önemli ölçüde aşarsa bu dolgu bir pigment olarak kabul edilebilir ancak 1.7’nin altında bir kırılma indisinde olan dolgu ve mineraller normal olarak dolgu maddesi olarak kabul edilir. Tablo 1.
Boya ve Polimer Performansını Etkileyen Dolgu Pigmentlerin Kritik Özellikleri
Dolguların temel etkileri aşağıdaki gibi kabaca sıralanabilir.
• Reolojik özellikleri kontrol etmek, örneğin uygulamadan sonra boya filminin akışını azaltmak için bir dereceye kadar jel bir yapı vermek,
• Daha iyi bir yapı kazandırmak için boyayı kalınlaştırmak ve aynı zamanda kutuda çökmeyi azaltmada yardımcı olmak,
• Astarlarda, filmin ‘açık’ kalması ve katlar arası yapışmanın iyileştirilmesi için bir miktar aşırı pigmentasyon sağlamak.
Bunun yanında boya ve polimerin performnsını etkileyen dolgu özellikleri özetle aşağıdaki gibi açıklanabilir.
Mineralojik Özellikler: Kimyasal bileşim, kristal yapı, Mohs sertliği.
Fiziksel Özellikler: Parlaklık, kırılma indisi, pH, inertlik, yağ emme, saflık ve çözünür tuzların varlığı.
Parçacık Özellikleri: Parçacık boyutu, şekli, boyut dağılımı ve en boy oranı.
Şekil 1. Minerallerin Mohs sertlikleri
Şekil 1’e göre, talk bir primer surfaser içinde zımparalama özelliklerini geliştirmek için daha iyi bir dolgu maddesi olurken, kuvars (SiO2) gibi bir silika bazlı dolgu sertliği nedeniyle bir iç mimari duvar boyasında daha iyi ovalama direnci sağlayacaktır.
Bir dolgunun kimyasal kompozisyonu, performans üzerindeki genel etkinin belirlenmesinde de büyük bir rol oynayabilir. Örneğin, dış lateks boyadaki kalsiyum karbonat asit yağmuru varlığında bozulabilir, bu da suda çözünür olan karbondioksit ve kalsiyum bikarbonat oluşturur.
Bu da filmin gözenekli olmasına ve kalsiyum bikarbonatın boya filminin yüzeyine geçmesi için çözünmez kalsiyum karbonatın hafif bir buzlanma oluşturmasına neden olur. pH değeri 7’nin altında olan dolgular, metal primerlerde kullanıldığında korozyonu şiddetlendirebilir.
Bir dolgudaki alüminyum, asitlik sağlarken, kalsiyum, potasyum, baryum ve sodyum alkalilik sağlar. Bir dolgu çözünür tuzlar içeriyorsa, bu tuzlar neme maruz kaldıklarında kabarmaya yardımcı olabilirler.
Bir dolgunun yağ emme değeri, temel olarak dolgu yüzey alanının, keten yağı tarafından ne kadar kolay ıslanabileceğinin bir fonksiyonudur. Düşük yağ emme özelliği, özellikle solvent kaynaklı boyalarda, düşük bağlayıcı gereksinimi ve düşük boya viskozitesi sağlar.
Pigmentin kırılma indisi (R.I.) ışığın bir ortamdan diğerine geçtiğinde nasıl kırıldığını ölçer. R.I ne kadar büyük olursa, ışık o kadar çok kırılır ve örtücülük de o kadar yüksek olur.
Dolguların çoğu, boya bağlayıcısına benzer bir kırılma indisindedir ve bu nedenle kürleşmiş filmde yüksek derecede örtücülüğe katkıda bulunmaz. İnce bir parçacık boyutunda olan alkali alüminyum silikat (nefalin) gibi bazı dolgu pigmentleri, TiO2 parçacık ara boşluklarına girerek örtücülüğe katkıda bulunur ve dolayısıyla daha düşük bir maliyette geliştirilmiş bir örtücülük sağlarlar. Tablo 1’de birkaç dolgu pigmentin bazı ortak özellikleri verilmiştir.
Tablo 1. En bilinen dolgu pigmentlerin fiziksel özellikleri
*OA=Oil absorption (yağ emme değeri)
Parçacık boyutu, büyüklük dağılımı ve biçim, dolguların boya performansı üzerinde ne gibi bir etkisinin olabileceğini belirlemede önemli bir rol oynayabilir. Şekil 2’de gösterilen parçacıklar, bir parçacık analizcisi tarafından belirtildiği gibi aynı “parçacık büyüklüğüne” sahip olabilir, ancak farklı fiziksel özellikler sağlayacaktır.
Bir iğnemsi ya da fiber parçacıktaki en boy oranı, ortalama uzunluğun ortalama çapa oranıdır (50 mikron uzunluğunda ve 5 mikron genişliğinde bir fiber dolgu, 10 en boy oranında olacaktır). Plakaya benzer bir parçacıktaki en boy oranı,plakanın yüzü ile aynı alandaki bir dairenin ortalama çapının, plakanın ortalama kalınlığına oranıdır.
İğne ya da iplik benzeri parçacıklar, özellikle yüzeye dik olarak yönlendirildiklerinde katlar arası yapışmayı artırma eğilimindedir; oysa, yüzeye paralel yönlendirilmişse plaka dolgular, yüzeyin oksijen ve nem geçirgenliğini en aza indirebilir. İkincisinin örnekleri mika ve mikamsı demir oksidi içerir.
Dolguların Üretimlerine Göre Sınıflandırılması
Doğal Dolgular
Doğal dolgu maddeleri başlıca silikatlar, karbonatlar ya da oksitlerdir. Hammadde olarak doğal yapıdaki dolgular, ya katı kayaç katmanları olarak çökeltiler biçiminde ya da granüler oluşumlar olarak bulunurlar.
Granül tipte olanlar genellikle hidrosiklonlar gibi fiziksel ayırma yöntemleriyle farklı parçacık büyüklüğüne ayrılırlar. Bunların yüzey alanları 1 ila 50 m2/g arasında olduğu için doğal dolgular, yarı aktifle aktif olmayan değerlerde değişen dolgulardır.
Bilinen Bazı Doğal DolgularSentetik Dolgular:
Bazı Sentetik Dolgular
Aktivitelerine Göre Dolgu Sınıflandırma: Elastomerlerde, bazı özel uygulamalar dışında, genellikle inorganik dolgu maddeleri kullanılır.
Dolgu maddesinin aktivitesine dayanarak ya da malzemenin üretim yöntemiyle ilgili sınıflandırma yapmak da olasıdır.
Öteki sınıflandırma kriterleri ise parçacık boyutu ve büyüklüğü, pH değeri ve rengin göreceli beyazlığıdır.
Dolgular, belirtilen bu sınıflar arasındaki fark keskin bir biçimde olmasa da,
• Aktif olmayan,
• Yarı aktif,
• Aktif olarak sınıflandırılabilir.
Tanım normal olarak, boyadaki dolgu maddesinin viskozite üzerinde etkisi ve çekme dayanımı, aşınma ve yırtılma direnci gibi mekanik özellikler üzerindeki etkisiyle ilişkilidir.
Tablo 2. Kırılma indisleri
Aktivite ve Üretim ile İlgili Sınıflandırma
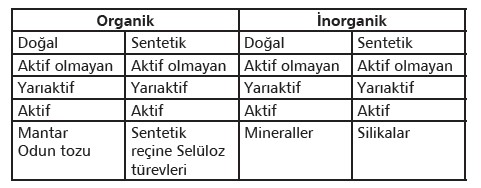
Genellikle, aktivite derecesinin, polimerle dolgu maddesi arasında ortaya çıkan etkileşim kuvvetlerinden etkilendiği varsayılmaktadır. Aktivitenin, özellikle beyaz dolgu maddelerinin ölçümünün yaygın bir yöntemi, azot adsorpsiyonudur: BET yüzeyinin m2/g’si olarak hesaplanır (BET=Brunauer Emmet ve Teller). Teorik olarak, bir parçacığın yüzey alanını, tanecik boyutuyla ilişkili bir kürenin matematiksel temelini kullanarak hesaplamak olasıdır.
Bununla birlikte, hesaplanan değerler genellikle adsorpsiyon yöntemleriyle elde edilen değerlerden daha küçüktür.
Adsorpsiyon yöntemi, daha gerçekçi olarak gerçek yüzey alanını gösterir. Hesaplanan ve ölçülen yüzey alanı arasındaki fark “iç yüzey alanı” olarak bilinir. Beyaz dolguları BET yüzeyine göre sınıflandırmak da mümkündür ancak yayınlanmış literatürlerde her durumda uygun aralıklara ilişkin bir anlaşmazlık söz konusu olmaktadır.
Genel olarak aktif dolgu maddeleri, bir bileşiğin özellikleri üzerinde aktif olmayan tipten daha fazla etki yapar. Çoğu durumda, aktif dolgu maddelerinden elde edilen optimum özellikler tam olarak minimum ya da maksimum bir dolgu maddesi girişi ile ilgilidir, buna karşın aktif olmayan dolgu maddeleri durumunda, özelliklerde bir değişim, giriş düzeyiyle orantılı olarak gelişir.
Genel olarak aktif dolgu maddeleri, bir bileşiğin özellikleri üzerinde aktif olmayan tipten daha fazla etkiye sahiptir.
Çoğu durumda, aktif dolgu maddelerinden elde edilen optimum özellikler tam olarak minimum ya da maksimum bir dolgu maddesi girişi ile ilgilidir, buna karşın aktif olmayan dolgu maddeleri durumunda, özelliklerde bir değişim giriş seviyesiyle doğru orantılı olarak gelişir.
Dolgu maddelerinin aktivitelerinin farklı polimerlerde karşılaştırılması, dolgu sınıflandırmasının BET yüzeyine göre yapılan sınıflandırmadan farklı olabileceğini göstermektedir. Bu durumda kimyasal bileşimin etkileri, dolgunun pH değeri, polimer tipi ve öteki bazı özellikleri önemlidir.
Genel olarak bir dolguyu BET yüzeyine göre sınıflandırmak gerçekten sadece teorik bir yönlendirmeyi gösterir. Pratik amaçlar için, özel bir polimerde ve özel bir uygulamada kullanılmak üzere bir dolgu maddesinin etkinliği yalnızca uygun test yöntemleriyle test edilerek belirlenir.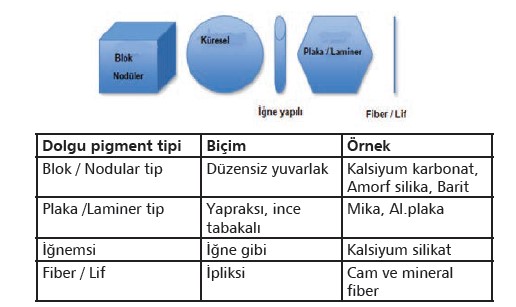
Şekil 2. Parçacık geometrisi, yapı ve parçacık boyutu biçimleri
Dolguların parçacık yapıları, normal olarak küresel, laminer ya da silindirik tiplerde sınıflandırılabilir. Polimerlerde dolgu maddesi olarak kullanılan silikatların temel kaynakları kaolinitlerdir (Al4(OH)8 [Si4O10] ya da A12O3 2SiO2 2H2O)‘dir. Kaolinitlerin yapısı laminerdir ve gerekirse ek sınıflandırma ile hidrokarbonlarla ayrılabilirler. Bunların ortalama parçacık büyüklükleri 1 ila 5 mikron arasındadır. Dolgu pigmentlerin boya ve kaplamlardaki rolü; dolgular, aşağıdaki özellikleri sağlamak ya da geliştirmek için boya ve kaplamalarda kullanılırlar.
Bir pigmentin ya da dolgunun emiciliği, kuşkusuz pigment partikülünün gözenekliği ile ilgilidir. Pigmentin bağlayıcısı, pigment yüzeyine emilir ve yüzeye adsorbe olur. Diatome silika gibi yüksek derecede emici malzemelerin yağ emme değerlerinin yüksek olmasının nedeni budur.
Primordial diatomların iskelet kalıntılarından üretilen bu malzemeler aynı zamanda matlaştırıcı olarak da yaygın kullanılmaktadır. Bununla birlikte, dolgular, tabloda görüldüğü gibi günümüzde boya üreticileri tarafından yalnızca dolgu ve matlaştırıcı olmaktan çok daha farklı amaçlar için kullanılmaktadır .
Parçacık Biçimi Nodüler/Blok Yapıda Olan Dolgular
Bir boyada pigment sistemi daha fazla bağlayıcı emerse (ve CPVC azalır), boyanın katı maddesi, oransal olarak bağlayıcı madde tüketen sistem viskozitede kaçınılmaz olarak artar.
Bir pigment sistemi düzenlendiğinde, daha fazla bağlayıcı emilir (ve CPVC azalır), katı madde miktarı ve nispeten bağlayıcı madde tüketen sistemde viskozite de kaçınılmaz olarak artar. Bunu gidermek için, hem katı madde miktarını azaltan hem de VOC’yi artıran bir çözücü eklenir.
Ancak bu durum, gerek maliyet açısından gerek giderek kısıtlayıcı düzenlemelerde istenen bir sonuç değildir. Bu nedenle, daha düşük yağ emme değeri olan dolguların gerçek avantajlar vardır. Bu, dolgu seçiminde temel gereklilik durumuna gelmiştir.
Parçacık Biçimi Laminer/Düz Plaka Olan Dolgular
Mika ve bazı talk ve clay gibi yassı, plaka tipi dolgular, yine silika, barit ya kalsiyum karbonat gibi nodüler dolgulara göre birim ağırlık başına çok yüksek yüzey alanlarından dolayı oldukça emicidirler. Bu dolgular, filmin mekanik özelliklerini, yan güçlendirme yoluyla geliştirme eğilimindedirler.
Aynı zamanda, bu tip düz plaka dolguların yalnızca filmi güçlendirmekle kalmayıp, aynı zamanda, pigmentin düzlemi boyunca gerilimin daha iyi dağılmasını sağlayarak iç gerilim birikmesini en aza indirdiği saptanmıştır. Mika içeren filmlerin gerilim dağıtma özelliklerinin olduğu belirlenmiştir.
Mika ve öteki düz plaka tipi dolgular, filmin iletim özelliklerini azaltmada bazı önemli değerler göstermiştir. Su, oksijen ve iyonik solüsyonların geçişini, en aza indirecek biçimde etki göstererek, plakaları üst üste binmesiyle bir bariyer sağlarlar.
Parçacık Biçimi Çubuk Yapıda Olan Dolgular
Çubuk kristal yapısıyla da benzersiz özellikteki wollastonitin bu yapısı, film dayanımının artmasına katkı yapar. Bu nedenle bu dolgu, cam elyafından yapılmış teknelerde, banyo armatürleri gibi yerlerde kullanılan jelkot kaplama polyester tabakalarının güçlendirilmesinde kullanılır.
Yassı, düz plaka yapılı dolgu pigmentlerle film güçlendirilmesi – özellikle wollastonit gibi çubuk parçacık biçimli dolgular, servis sırasında çatlamayı önlemek için güçlendirme gerektiren birçok boya ve kaplama türünde önerilir.
Bu yapışma gücü kaybı, yaşlanmayla ya da UV ya da öteki bozucu radyasyon etkisinde kalma sonucu filmin gevrekleşmesinin bir sonucu olarak ortaya çıktığında özellikle tehlikelidir. Yaşlanma üzerinde çapraz bağlanma eğiliminde olan oksitleyici sistemler, uygun şekilde güçlendirilmedikçe çatlamaya neden olur.
Çubuklar, plakalardan ya da lif yapıda olanlardan daha düşük yüzey alanındadır ve bu nedenle, çubuk kristalli wollastonit ile güçlendirmenin, viskozitenin azalması üzerinde daha az olumsuz bir etkide olması ve plaka yapıdaki dolguların kullanımından daha düşük VOC değerine olanak sağlaması şaşırtıcı değildir.
Parçacık Biçimi Lifli (Elyaf) Yapıda Olan Dolgular
Lifli yapıda olan dolgular ki bunlardan özellikle asbest, uzun yıllar güçlendirici dolgu maddesi olarak kullanılmıştır. Bu konuda, çubuk yapıdaki dolgularla aynı şekilde işlev görüyorlardı.
Lifli asbest, ışığa duyarlı (asfalt) sonkatlarda, özellikle elyafların boya ya da kaplamayı bir arada tuttuğu çatı kaplamalarında, UV ışığın etkisinde kaldığında kürleşmiş filmin yüzeyinde çatlama ve timsah derisine benzer bir yapı oluşmasını önleyen bir dolgu olarak yaygın olarak kullanılmıştır.
Toksik durumu nedeniyle asbestin endüstride terk edilmesinden sonra, mineral bazlı olmayan dolgular kullanılmıştır. Elyaflı poliolefin hamurları, Kevlar®, akrilikler ve selülozikler bu tür dolgu maddelerinin örnekleridir.
Lifli dolguların uygulamalar arasında blok dolgu maddeleri, eklem bileşikleri, dokulu ve özel efektli boyalar ve çatı kaplamaları bulunur.
Selülozik malzemeler ve yüksek en boy oranında olan mikrofiber uzatma maddeleri (wollastonit) gibi hamurların kombinasyonları, asbestli çatı kaplamalarında asbest yerine güçlendirici maddeler olarak kullanılmıştır.
Güçlendirici özelliklerin yanı sıra sızdırmazlık özelliklerinde de olan mika, duvar levhalarında bağlama bileşiklerinde de yaygın olarak kullanılmaktadır.
Dolgularda Sertlik
Dolgulardaki bir başka önemli özellik ise mineralin sertliğidir. En sert dolgular ağırlıklı olarak silikalar olup, özellikle kuvars tipi kristal silikalardır.
Bu malzemeler, boya ve kaplamaların sertliğini ve aşınma direncini artırmak, iç kullanımlı emülsiyon boyalarda optimum fırçalama ve aşınma direnci ile zemin kaplamalarında ve bakım boyalarında aşınma direnci sağlamak için kullanılır.
Bunların film yüzeyinin üzerinde görülebilen kaba tipleri, kat üstüne kat atılabilen astarlara mükemmel “diş” verecektir.
Zemin kaplamalarında kullanılan aynı kristal malzemelerin mikronize versiyonları olan “amorf” silisler de bu şekilde kullanılır. Kaymanın muhtemel olduğu durumlarda, ilave iri kristalimsi silisler, kurumadan önce ıslak filme yayılabilir, aşırı “bağlanmamış” malzeme, zemin kat kuruduktan sonra zeminden süpürülür.
Bununla birlikte, serbest silikanın toksikolojik tehlikeleri, son yıllarda, bu tür malzemelerin kaplamalarda kullanımını sınırlandırmaya başlamıştır. Silikadan biraz daha az sert olan nefelin siyenit ve wollastonittir.
Bu malzemeler silika için uygun bir alternatif olarak değerlendirilebilir ve wollastonit son zamanlarda trafik boyalarında önem kazanmaya başlamıştır.
Dolgularda Kimyasal Etkiler
Dolguların fiziksel yönleri, boyalarda kullanımları için özellikle önemlidir, ancak fiziksel yönleri kadar kimyasal yapıları da önemlidir. Dolgular bir zamanlar inert pigmentler olarak sınıflandırılmıştır. Bugün bunun doğru olmadığını biliyoruz. Kalsiyum karbonat ya da tebeşir gibi bazı dolgular asitlerden kolayca etkilenirler.
Bu nedenle, reaksiyona girebilecekleri karboksile viniller, su bazlı alkidler gibi alkali-duyarlı sistemlerin pigmentasyonunda ya da asidik ortamlarda bulunacak sistemlerin pigmentasyonunda bunlardan kaçınılmalıdır.
Asit katalizli sistemler, eğer böyle alkali pigmentler kullanılıyorsa, katalizör düzeyinde bir miktar ayarlama gerektirecektir. Alkali dolgu maddelerinin, demir mavisi gibi alkali duyarlı renk pigmentleriyle birlikte kullanılmaması için de özen gösterilmelidir.
Alkalin pigmentler içeren filmler, çözünebilir demir ve bakır bileşikleri tarafından lekelenmeye de duyarlıdır. Dolguların çözünmesi ve ardından tuzlarının asidik ortamlar ile filmden ayrılması filmi zayıflatma eğiliminde olacaktır.
Bu aynı zamanda, kalsiyum sülfat tuzlarının koyu renkli filmler üzerinde çözünür tuzların yağmurla çözülmesinin mümkün olmadığı yerlerde beyaz kristal bir tortu olarak birikme eğiliminde olduğu ve donma gibi başka kusurlara da yol açabilir.
Korozyona dirençli yardımcı bir dolgu pigment olarak yine de wollastonit daha yararlıdır. Bu dolgu, oldukça bazik olmasına karşın, ne çözünebilir ne de karbonat gibi aside duyarlı değildir.
Wollastonite, epoksi sistemlerinde asit dayanımı için başarıyla bir dolgu olarak kullanılmıştır, ancak gelişmiş pasiflik için metal primerlerde gereken pH kontrol derecesini sağlayacak kadar yeterli düzeyde çözünür.
Bu bağlamda, wollastonit gerekli olan pasifleşmeyi sağlamak için daha pahalı korozyon engelleyici pigmentlerin kullanım düzeylerini düşürmek için kullanılmış olan antikorozif sistemlerde yardımcı bir pigment olarak başarıyla kullanılmıştır.
Ayrıca, alüminyum plaka gibi, yassı, plaka yapıda (yüksek geçirimsiz) asal pigmentlerle birlikte wollastonit kombine edilerek bariyer sistemlerde kullanım alanı bulur. Mika aynı zamanda alüminyumlu bariyer sistemleri için bir dolgu olarak da kullanılmıştır.
Ağırlıkça %25’e kadar verilen alüminyum plakalar, korozyon direnci üzerinde zararlı etkileri olmadan mika ile yer değiştirmiştir. Mika, alüminyumdan daha iyi kimyasal dayanımda olduğu için, bu cihaz, filmin aşırı pH derecelerine ulaştığı durumlarda özellikle önem kazanır.
Bariyer sistemlerde hidrofillik derecesi, china clay gibi “su seven” dolgu pigmentler filme su girme eğiliminde olacağından, kontrol edilmelidir. Bu nedenle mika ve plaka yapıdaki talk ve kloritler, bariyer sistemlerde china clay’den çok daha fazla kullanılır.
Öte yandan, china clay’ler anti korozif sistemlerde daha etkili bir biçimde kullanılabilir. Talk gibi plaka yapıda olan china clay’lerin de filmi güçlendirme eğiliminde olduğu ve endüstriyel astarların zımparalanmasını iyileştirdiği saptanmıştır. Geçmişte boyalarda kullanılan bazı malzemelerin suda çözünürlüğü oldukça yüksektir.
Susuz kalsiyum sülfat bu kategoriye girer. Şimdilerde kullanımı çok azalmıştır, ancak uzun yıllar TiO2 ile bir kompleks olarak kullanılmıştır.
Baritler, mükemmel emaye tutma özellikleri veren inert bir nodüler pigmenttir. Baritler iki şekilde bulunur. Bunlar, doğal olarak öğütülmüş baritler ve daha az yaygın kullanılan ancak daha beyaz olan presipite tip baritlerdir.
Presipite baritler, genellikle yağ emme değerleri doğal baritlerden daha yüksek ve daha ince parçacık boyutundadır. “Blanc fix” olarak bilinen daha yumuşak presipite tip barit kolayca disperse olur ve oto tamir astarlarında ve parlak sistemlerin astarlarında yaygın olarak kullanılır.
Barit, en düşük yağ emme özelliğinde olan en ağır dolgudur. Düşük VOC sistemlerinde yaygın olarak kullanılır, ancak çökmesini kontrol etmek için ek destek gerekebilir.
Dolguların Örtücülük Üzerine Etkisi
Dolgular boya filminin gerçek örtücülüğünü ya da rengini artırmaz. Opaklık yani örtücülük, pigment ve bağlayıcı arasındaki arayüzlerde film içinde kırılan ve saçılan ışık demetlerinin fiziksel bir etkisidir. Işık ne kadar çok kırılırsa, ışığın film boyunca geçişi o kadar düşük olacaktır ve opaklık o kadar fazla olacaktır.
Işık, bu ara yüzün her iki tarafındaki pigment ile bağlayıcı arasında büyük bir kırılma indisi farkı olduğunda, ışık daha büyük ölçüde kırılır.
En yüksek örtücülük verimliliğini elde etmek için daha karmaşık bir yol olan TiO2’nin bitişik parçacıklarını ayırmak için delamine edilmiş yani tabakalara ayrılmış kaolin (kalsine kaolin) plakalarının kullanılmasıdır.
Bunun gerçekleşmesi için, bitişik her TiO2 partikülünün, belirlenen dalga boyunda aynı noktada ışık dalga boyunu durdurması gerekir. Işığın dalga boyu, en uygun biçimde disperse edilmiş bir TiO2 partikülünün (0.25m) çapından ortalama olarak bir miktar (0.4-0.7m) büyük olduğundan, iki bitişik partikül arasındaki uzaklığı merkeze yükseltmek için ara plakaları kullanmak gerekir.
TiO2 böylece bir tam dalga boyuna eşit olur. Sistem karmaşık olmasına karşın etkili olarak çalışır ve birçok iç mimari boyada kullanılır.
Dolguların Öteki Kullanım Alanları
Dolgular boya ve kaplamalar dışında öteki endüstrilerde de yaygın olarak kullanılır. Bunlara örnek olarak plastikler, seramikler, kauçuklar, yapıştırıcılar ve sızdırmazlık maddeleri, madencilik, kozmetikler ve asfalt üretimi sayılabilir.
Kağıt üretiminde dolgu kullanımı özellikle önemlidir. Burada asidik kâğıt yapma işlemleri alkali sistemlere yol açtığından china clay ve kalsiyum karbonat gibi malzemeler kullanılmaktadır.
Mehmet Namık Kayaalp
Kimya Mühendisi
Ecelak Boya Kimya Ltd. Şti.
Kaynakça
1. Paint Formulation, by J.Boxall and J.A.von Fraunhofer. Gorge Godvin Limited, London
2. Jocca, Oil, Colours Chemists’Association-London 1966
3. Hoffmann Minerals
4. Payne, H.F. “Organic Coatings Technology,” Vol II, p.773-804, Wiley, NY. 1961.
5. Extenders, By Clive Hare / Coating System Design Inc., Lakeville, MA and Roland Beck / Manager, Marketing, NYCO Minerals Inc., Calgary, Alberta, Canada
6. Prospector Knowledge Center, Ronald J. Lewarchik, President and CEO of Chemical Dynamics, LLC,