Investigation of Infrared Curing as an Alternative Composite Production Method to Autoclave
Composite materials are increasingly used in many areas such as marine, aerospace, automotive and defense industries. Especially with the decrease in production costs and raw material prices and the development of different production methods, the market share and usage areas of composite products started to increase.
One of the most common types of composite materials is polymer matrix composite materials. Today, the most common type of fiber used in polymer matrix composite materials is glass fiber.
The main reason for this is low raw material costs. Although they have limited usage area, carbon fiber reinforced composite materials are widely used in cases where advanced mechanical properties are desired.
Nowadays, autoclave curing is the most advanced production method in which high quality polymer matrix composites are obtained which will satisfy the aviation industry. The autoclave, a temperature and pressure furnace – especially with the growth of dimensions – has high initial investment costs and operating costs.
Therefore, academic and industrial studies on the development of non-autoclave production methods have started to increase. For instance, microwave curing [1], laser curing [2], electron beam [3], ultraviolet rays [4], induction curing [5], resistance heating [6] production methods are being developed.
One of the biggest problems encountered in the application of alternative methods to autoclave is that the heating is not homogeneous, and the other is that the method is not sustainable – products of the same quality can not be obtained continuously-.
In this study, the applicability of infrared curing process for polymer matrix composite which is an alternative to autoclave is investigated. The wavelengths of infrared rays range from 0.7 microns to 1 mm, and for industrial heating purposes, 1 micron to 15 microns wavelengths are often used.
The main reason why infrared curing is proposed as an alternative production method to autoclave is the potential to shorten the curing time. In a study performed in France [7], it was determined that infrared curing can provide a 40% to 70% improvement in curing time.
Reducing curing times, which is one of the important cost items of autoclave curing, will reduce the total operating costs of the process. It is also an important advantage that heating speeds can be set much easier. One of the biggest problems in infrared curing is homogeneous heating.
The temperature distribution along the surface of the material and throughout the thickness should be tested and the process parameters evaluated accordingly.
Another aim of the study is to perform curing cycle tests with a thickness to be selected considering the predetermined temperature distributions.
For this purpose, a Programmable Logical Controller (PLC) system, in which temperature distributions can be monitored, is integrated into the infrared curing unit and the temperatures are recorded with a thermal imager at regular intervals.
As shown in Figure 1, the temperature distribution of the carbon fiber prepreg material, which was divided into 9 different regions, at full power without any interference to the power of the lamp, was monitored both along the surface and throughout the thickness.
Twill braided carbon fiber reinforced prepreg materials with OM11 resin system manufactured by Kordsa were used in the experiments. The recommended curing cycle of the material for the autoclave is as in Figure 2.
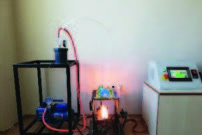
Figure 1. Experimental setup of infrared curing
Figure 2. Recommended curing cycle for the autoclave of prepreg material
According to the data obtained from the studies, it was observed that the carbon fiber prepreg material heated by a working lamp at the related wavelengths provides homogeneous temperature distribution up to a certain thickness.
This means that for the parts thicker than this thickness, heat transfer is by conduction, not by radiation. Therefore, the layers in the inner zones will heat up later and this will result in residual stresses and cause material distortion.
Observations along the surface of the material revealed that temperatures in the middle of the material were up to 15% higher on average.
At this point, the selection of the region that can best represent the overall temperature of the material is important. Because the PLC system which will be used for curing cycle tests needs a single temperature value in order to make the power control to provide the desired curing parameters.
Therefore, since the thermocouple to be placed at the wrong point does not accurately represent the general temperature distribution on the material and it will not be possible to apply the given curing cycle correctly.
In the second phase of the study, productions were made in different curing cycles and these products were subjected to tensile tests. Three different process parameters were used in the tests: heating speed, maximum temperature and plateau time (maximum temperature residence time).
A total of 25 cure cycles were determined by assigning 5 different values to each parameter using the Taguchi experimental design method. Considering the test results, the most suitable curing cycle for the infrared curing process was obtained. The cycle is completed in approximately 80 minutes.
This time is 38% shorter than the recommended curing cycle time for autoclave curing process which is 130 minutes. When the tensile test results are examined, the tensile strength value of the material after autoclave curing is 835 MPa, while the tensile strength values of the samples applied above curing cycle by infrared are 800 MPa. The above results show that the infrared curing process has the potential to be a successful alternative to autoclave.
Especially in the case of infrared curing which can be used successfully in the production of thin laminated sheets and sandwich plates, it is thought that if the whole process is modeled with scientific studies and homogenous heating is provided, aviation quality products can be produced at much lower costs than autoclave.
Mert Kılınçel – Genel Müdür – General Manager – Numerics Composites – Müh. Mak. San. Tic. Ltd. Şti.
Yakup Okan Alpay – Ar-Ge Müdürü – R&D Manager – Numerics Composites – Müh. Mak. San. Tic. Ltd. Şti.