Introducing Hardcoat to Polycarbonate Surfaces
Polycarbonate plastics are normally amorphous and transparent thermoplastics. In market, processed polycarbonate is an alternative to glass in various colors both as transparent or translucent.
Transparent and impact resistant polycarbonate sheets can be used in the construction of
different materials. It is widely used in bulletproof glasses, eyeglasses, medical devices, automotive parts, greenhouses, digital floppy disks, CDs and outdoor lighting fixtures.
Polycarbonate is generally preferred as the most realistic imitation of glass and provides great convenience for the manufacturer.
For example, the use of rectangular and round glasses, which were generally used in various countries in the 1980s in automotive headlight manufacturing, were abolished as they caused aerodynamic concerns and in terms of pedestrian safety.
These headlight types were generally produced from glass material, and since then,
polycarbonate lenses have been used instead of glass materials.
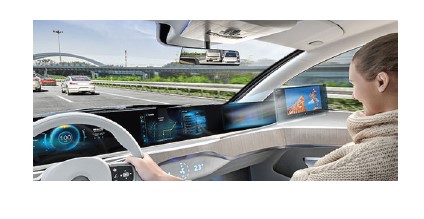
Of course, besides the production and cost conveniences it provides, there are also some disadvantages of polycarbonate surfaces compared to glass. Since glass provides a very
hard surface stability, it is not easily scratched. As polycarbonates are thermoplastic in nature, they can be scratched when facing severe strength.
Glasses do not turn yellow under sunlight due to their strong UV resistance, but polycarbonate surfaces can turn yellow under long-term sunlight. We try to eliminate the problems with chemical materials and applications developed to solve such problems.
The application called hardcoat is basically a chemical coating method developed to solve the above problems. By coating the surface with a silicone-containing coating material, it gains high resistance to environmental effects, UV light and physical interventions.
Automation can be set up to suit for the preferred functionally on the production line. It is compatible with all types of applications; whether by robotic spraying, deep immersion or ink jet method. In order to cure the material, it is possible to cure under high temperature in an oven, and if a faster curing is requested, it is possible to cure under UV light at a certain wavelength for much shorter times.
In particular, the automotive industry uses engineering plastics if they can certify the specific specifications for meeting certain norms. At this point, the inspection and approval process are very critical.
Hardcoat materials produced under the brand name of Momentive Performance Materials are ASTM D 1003/1044 approved products that have successfully passed 3, 5 and 10 years of tests in Florida and Arizona conditions where microcrack and yellowing resistance
are measured.
We can provide a great advantage in your production with Momentive Hardcoat materials,
which can adhere to all plexiglass and polycarbonate surfaces without the need to use a surface preparation primer.
Alper Bağ
Chemical Solution Explorer
Latro Kimya