In this study, membranes that can appeal to the sealing industry were obtained by nanotechnological electrospinning technique containing activated charcoal reinforced polyvinylidene fluoride (PVDF) polymer.
Activated charcoal is made from the waste materials of shoe manufacturers, which are found as waste in our environment. Waste materials were brought into suitable powder form with the grinding process after pyrolysis.
Composite solutions were formed by reinforcing powders of appropriate size with 1%, 5% and 8% PVDF polymer solution. Impermeable membranes were obtained from the solutions with the help of electric field. This method is easy, inexpensive and sustainable. It can be
easily integrated into target applications for sealing and filtering purposes.
1. Introduction
The concept of impermeability is the absence of any infiltration into areas strictly separated by borders. In this way, it will fulfill its purpose. For this purpose, sealing elements such as clamps, oil, pipes, plates and membranes are used in sectoral applications [1].
The leaking problem is undesirable in most industries. After a flow, the performance of the products may decrease, causing tearing, poor quality and undesirable problems. In addition, if leakage is considered to be of vital importance, it causes a situation that can lead to electric shocks and death of people [2].
While finding many production methodologies for sealing materials, the fact that the raw materials to be used are expensive and come from abroad cannot partially ensure sustainability. However, our main emphasis in our study is to encourage the use of waste
materials in many applications. Because wastes negatively affect our environment and us indirectly. It is important to recycle waste materials and create qualified products by recycling. The most notable of these production systems is nanotechnological electrospinning[3].
Nanotechnological electrospinning is the technique of producing nanofiber membranes from polymer solutions with the help of electric field. It is a system that offers purposeful use in almost all sectors such as health, cosmetics, food, filtration and defense. The system simply consists of the syringe pump, power supply and collector plate. It is the simplest and cheapest technique of forming fiber. It is nanotechnological production that can provide the highest performance in sealing applications [4]. Superior impermeability can be achieved by showing optimum membrane quality with the desired active substance, polymer usage and production parameters for the purpose. Taylor cone and nanofiber image are shown in Figure 1.1.
Polyvinylidene fluoride (PVDF) polymer is a hydrophobic water-repellent membrane. It is a polymer that is frequently preferred in filter applications and can provide superior strength and sealing performance. In sealing applications, it can adapt to the platform it is on
thanks to its appropriate elastic feature. The chemical structure of PVDF is given in Figure 1.2.
performance will be achieved with impermeable and filterable membranes.
2. Material and Method
2.1 Material
In our study, fire shoe insoles were collected for the production of activated charcoal. PVDF polymer was taken from recycling companies in the sector. In the nanotechnological electrospinning system, oiled paper was preferred as the backing material. Dimethylformamide(DMF) solvent was used to dissolve the PVDF polymer.
2.2. Method
2.2.1 Collection of Fire Shoes
Waste shoe soles were collected from the materials of a shoe sole manufacturer operating in Istanbul. And transferred to the production area to be pyrolyzed. Waste shoe rubber soles are shown in Figure 2.1.
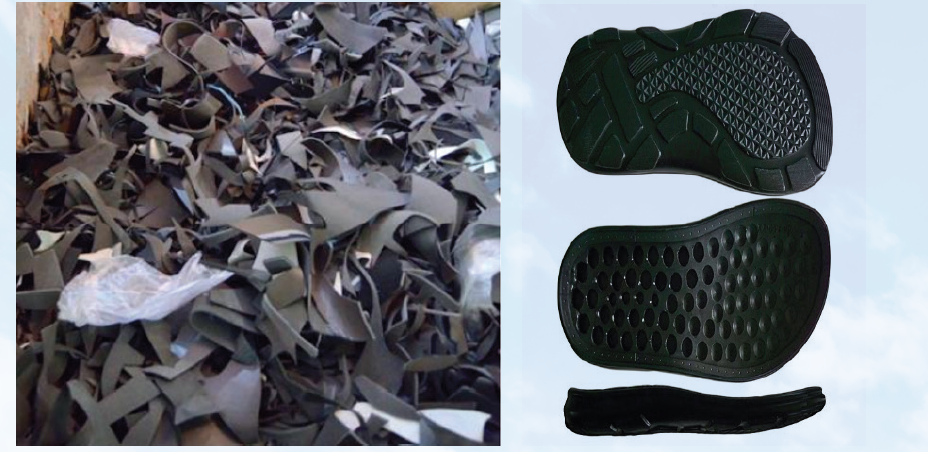
2.2.2 Pyrolysis of Fire Shoe Insoles and Production of Activated Charcoal
The collected wastes were put into the pyrolysis machine and burned by heating. After the combustion process, coal particles were obtained. The coal particles were first brought to the appropriate powder form in the ceramic mortar and then in the ball mill. As the time
increased, the dimensions decreased and were brought to a powder size of 40 micrometers. Activated charcoal was obtained and made ready for membrane production.
The pyrolysis of Fire shoe insoles and the production of activated charcoal are shown in Figure 2.2.
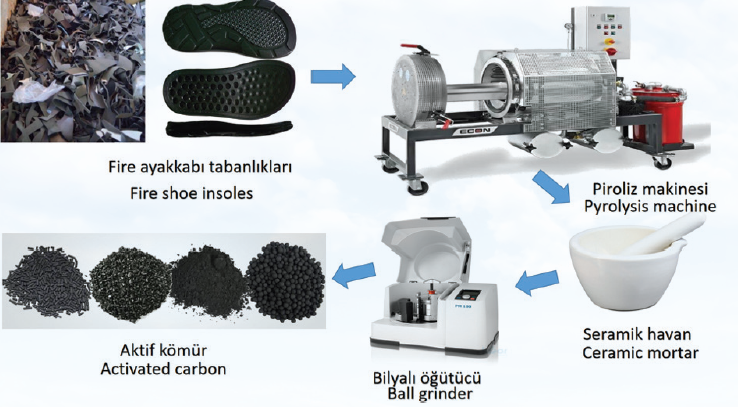
2.2.3 Production of Nanotechnological Membrane Containing Activated Charcoal
The activated charcoal obtained was weighed 1, 5 and 8 mg on a precision balance. 10 grams of PVDF was weighed and dissolved in 100 ml of DMF solvent by mixing
with the help of a magnetic stirrer at 60oC for 12 hours. Composite solutions were obtained by reinforcing the weighed activated charcoal into the solutions. In the nanotechnological electrospinning system, oiled paper was used as the backing material. Membranes were obtained by choosing 1-2.5 ml feed rate, 25-30 kV high voltage and 12-15 cm working distance as working parameters. Figure 2.3 shows the stages of nanotechnological membrane production containing activated charcoal.
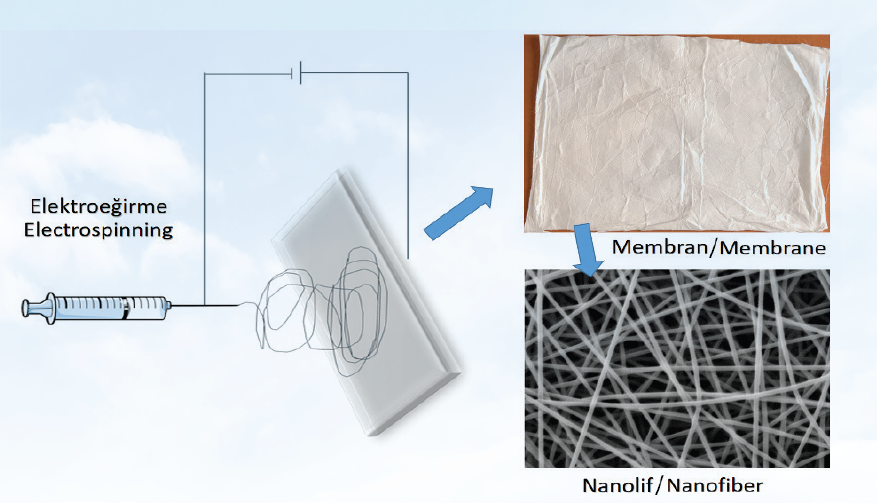
According to the contact angle measurement result, 135° droplets were detected and it was determined to be superhydrophobic and super water repellent. While measuring 45 MPa according to the PVDF membrane mechanical properties, the mechanical properties improved as the activated charcoal increased. The highest 57 MPa value was determined in the 8% added activated charcoal composition.
4. Conclusions
In our study, activated charcoal was successfully obtained from the insoles of fire shoes by pyrolysis. This ratio enabled the production of 75% activated charcoal from the wastes. Nanofiber membranes have been successfully obtained with the nanotechnological electrospinning technique. Useful products can be produced from wastes. The aim is to produce qualified products by using our own domestic resources without being dependent
on foreign sources.
In our study, we preferred to use waste materials, which are a serious problem for shoe manufacturers and the environment. Because these materials are thermoset and non-recyclable, they do not melt and are a serious burden for the environment. It increases the carbon footprint. For this reason, we wanted to draw attention to this area and high-performance membranes that can be impermeable and filtered are easily provided with
the use of nanotechnology. There are organizations in our environment, such as shoe sole manufacturers, that significantly increase their carbon footprint. With a serious structuring and qualified project design, waste materials can be transformed into added value.
References
[1] Akıncı, A. (1997). Sızdırmazlık elemanlarının yapı ve özellikleri.
[2] TOPAL, O. (2023). TÜRKİYE’DE ELEKTRİKLİ VE HİBRİT ARAÇLAR İÇİN ACİL MÜDAHALE YAKLAŞIMLARI. Çevre Şehir ve İklim Dergisi, 2(3), 190-206. [3] Buluş, E., Buluş, G. S., & Yakuphanoglu, F. (2020). Production of polylactic acid-activated charcoal nanofiber membranes
for COVID-19 pandemic by electrospinning technique and determination of filtration efficiency. Journal of Materials and Electronic Devices, 4(1), 21-26. [4] DOĞANCI, E., DOĞANCI, M. D., BULUŞ, G. S., & BULUŞ, E. (2023). Polylactic Acide-Activated Coal Electrospun Mat Production and Characterization. Düzce Üniversitesi Bilim ve Teknoloji Dergisi, 11(3), 1365-1377. [5] Kausar, A., Ahmad, I., Aldaghri, O., Ibnaouf, K. H., & Eisa, M. H. (2023). Nanoclay-Reinforced Nanocomposite Nanofibers—
Fundamentals and State-of-the-Art Developments. Minerals, 13(6), 817. [6] Kocabıyık, B. (2023). Siyez (Triticum Monococcum L.) buğdayı kavuzundan elde edilen aktif karbon kullanılarak kirleticilerin
sulu çözeltilerden adsorpsiyon metoduyla uzaklaşıtırılması. [7] Mohammadpourfazeli, S., Arash, S., Ansari, A., Yang, S., Mallick, K., & Bagherzadeh, R. (2023). Future prospects and recent developments of polyvinylidene fluoride (PVDF) piezoelectric polymer; fabrication methods, structure, and electro-mechanical properties. RSC advances, 13(1), 370-387.
Erdi Buluş
Lecturer / Material Technologies Specialist
Istanbul Arel University
ArelPOTKAM (Polymer Technologies and Composite
Application and Research Center)
Department of Transportation Services, Civil Aviation
Cabin Services Program / Vocational School
Gülseren Sakarya Buluş
Specialist
Istanbul Provincial Health Directorate
Bahçeşehir University
Engineering Management Department
Graduate School of Education